Oskar Zięta, a Polish architect and designer, began working on a technology that would allow the production of single-material, air-filled metal objects nearly 20 years ago. Today, he is the multidisciplinary head of the design firm ZIETA Studio, and together with his team, he uses this innovative technology not only to make furniture, but also to create art and architectural installations. The futuristic-looking inflatable metal objects—of which the PLOPP chair is the most well known—can be mass-produced, but no two pieces will ever look exactly the same, as each piece curves slightly differently when filled with air. We asked the designer about the so-called FiDU technology and the challenges of design today.
You’re one of the designers with a specific manufacturing technology attached to your name, the so-called FiDU technology, which creates metal objects that resemble inflated balloons. Can you briefly tell us about the essence of the technology and your first experiments?
FiDU (short for Freie Innendruck Umformung in German) is a method of making different sized objects from two-dimensional (2.5) welded metal sheets, which in the process transform into three-dimensional objects by internal pressure. This deformation process results in an increase in volume. The production files required for the 2.5 D form take up only a few kilobytes, which of course means that we do not exactly know what the final shape of the object will be. If we wanted to produce the same final shape using traditional manufacturing methods, it would require several gigabytes of data.
FiDU technology, which I have been working on for nearly 20 years, is based on metal. Sheet metal is one of the most advanced materials today, used in the automotive, aerospace, chemical and even the household appliance industries. Few design studios work with sheet metal today, and we are respectful of the material’s properties and its freedom of movement. We don’t want to completely control the molding process, but to preserve the true face of sheet metal by respecting anisotropy and internal material structure. For us, it is really the process that results in the uniqueness of the structures.
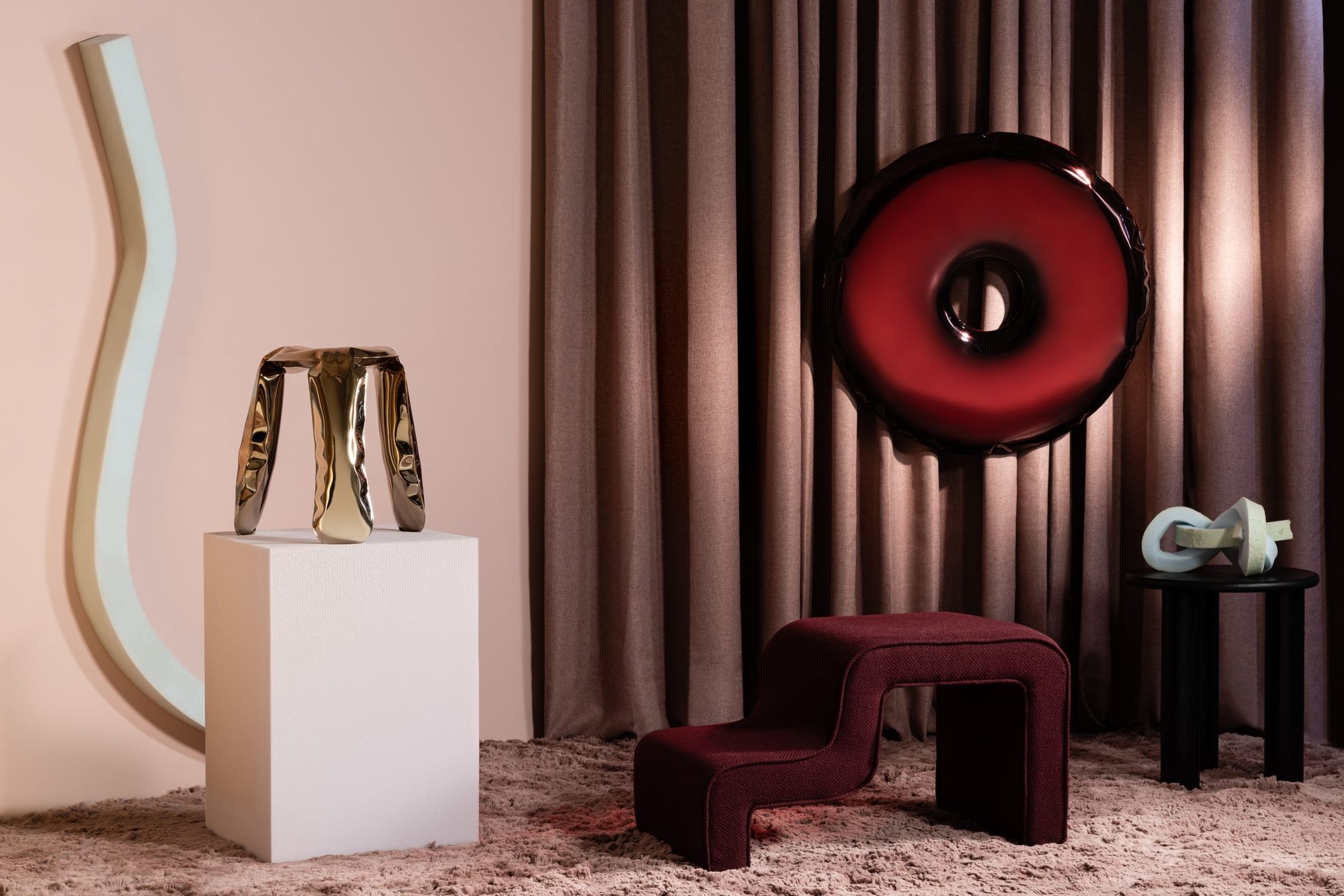
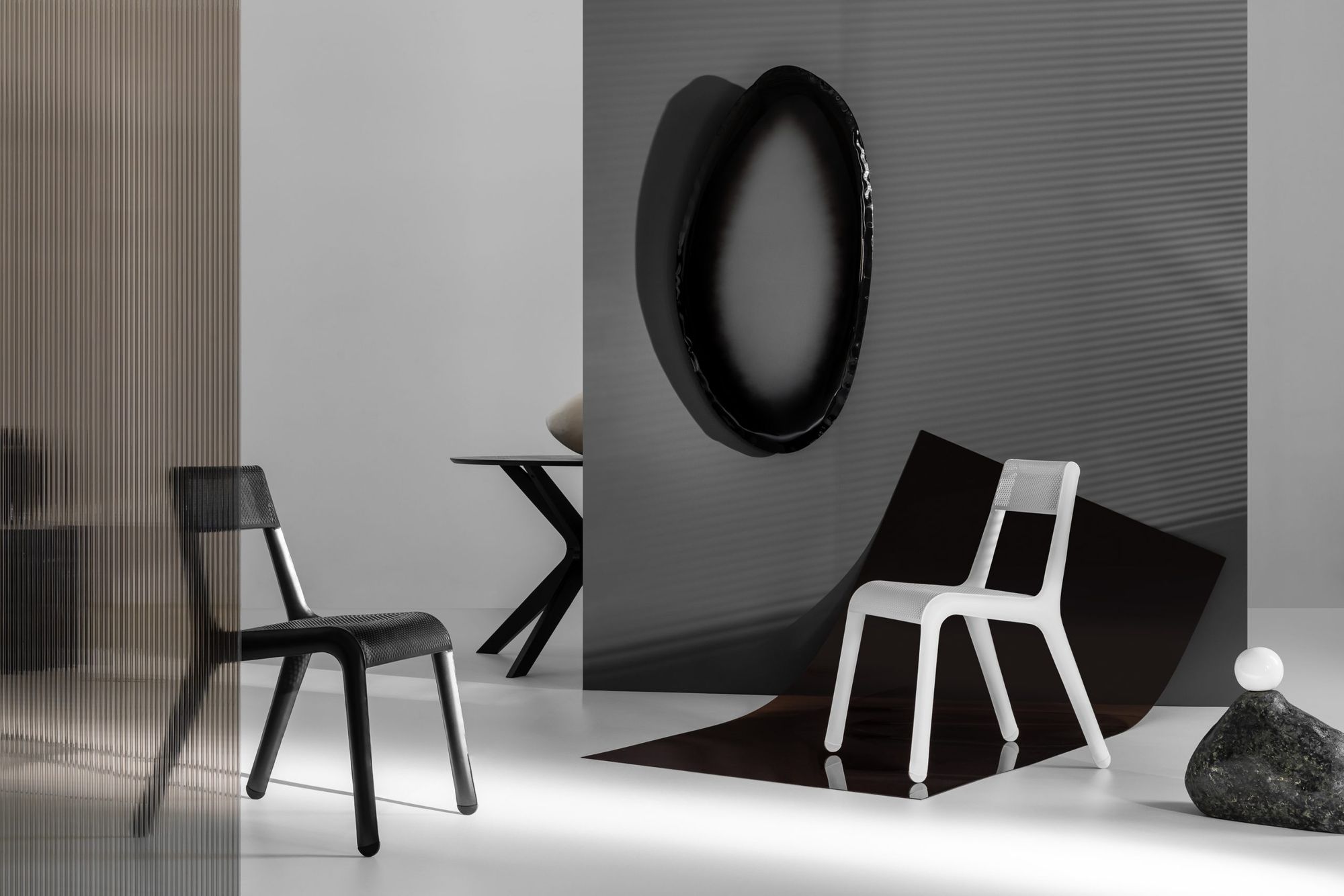
In a previous article, I read that FiDU technology could be used to make larger objects that could be utilized by the transport or energy industries. Although larger objects have been made at ZIETA Studio, they were mostly created for artistic projects. Do you now plan to use the technology to make urban infrastructure objects?
Yes, we are constantly working on such solutions. We have a lot of work waiting to be revealed to the public. FiDU is characterized by its ability to create very light, durable and unique shapes without expensive tools and molding. This has great potential. Our Blow & Roll installation, for example, is made of rolled steel sections that can be inflated anywhere and transformed into durable and ultra-light three-dimensional tubes. Elements like this are useful in many industries, including the aerospace industry. And during the construction of our Nawa and Wir projects, we proved that FiDU technology has a future in architecture.
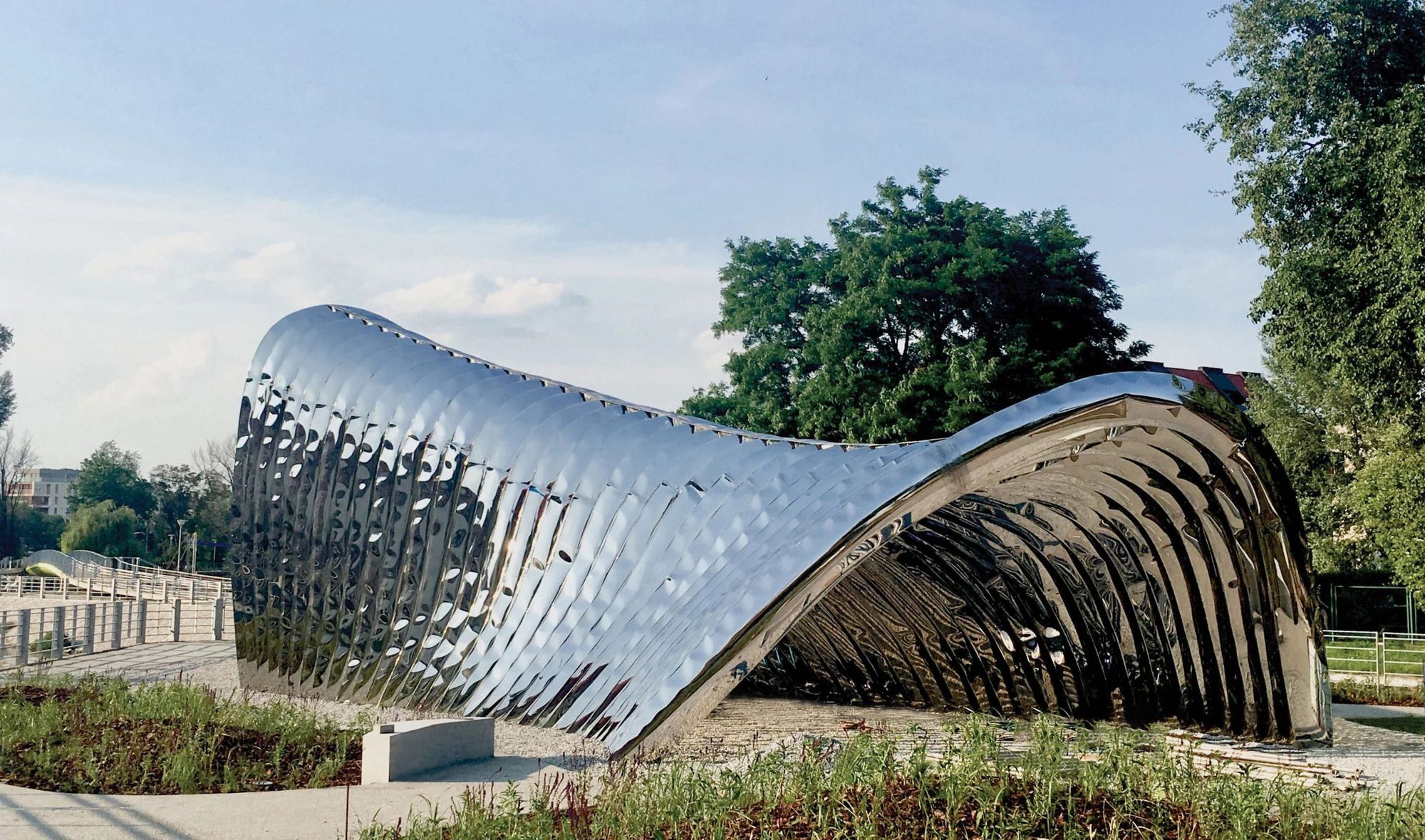
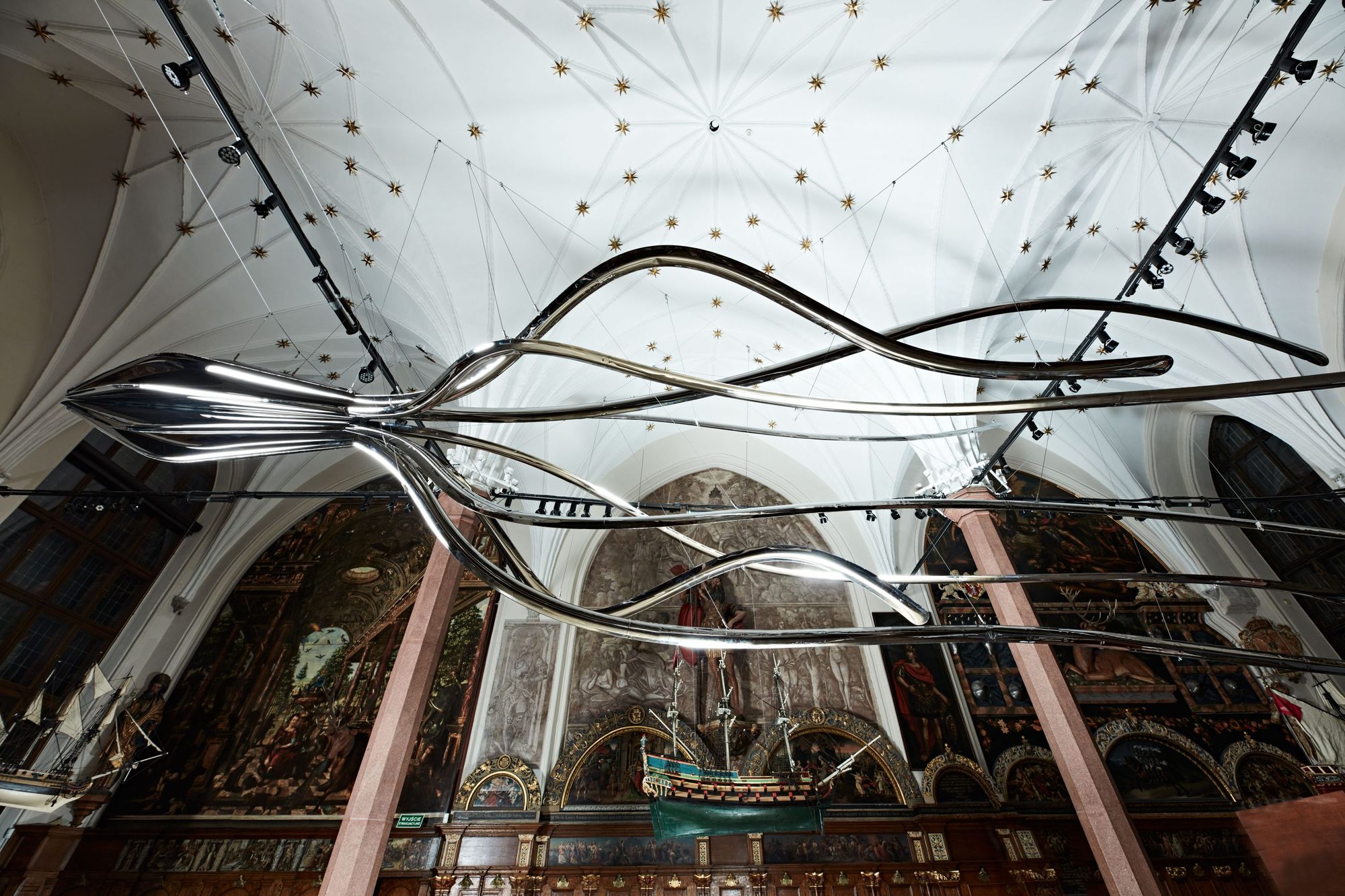
Do you have a role model from design history (or even from the contemporary scene) whose work inspires you?
In 1957, Italian designer Gio Ponti created the Superleggera chair, which weighed only 1700 grams. He inspired me to try my hand at creating the lightest chair I could. In 2019, the studio and I were able to present the ULTRALEGGERA chair, which is even lighter than Ponti’s creation, weighing 1660 grams and is both a sturdy and modern piece of furniture.
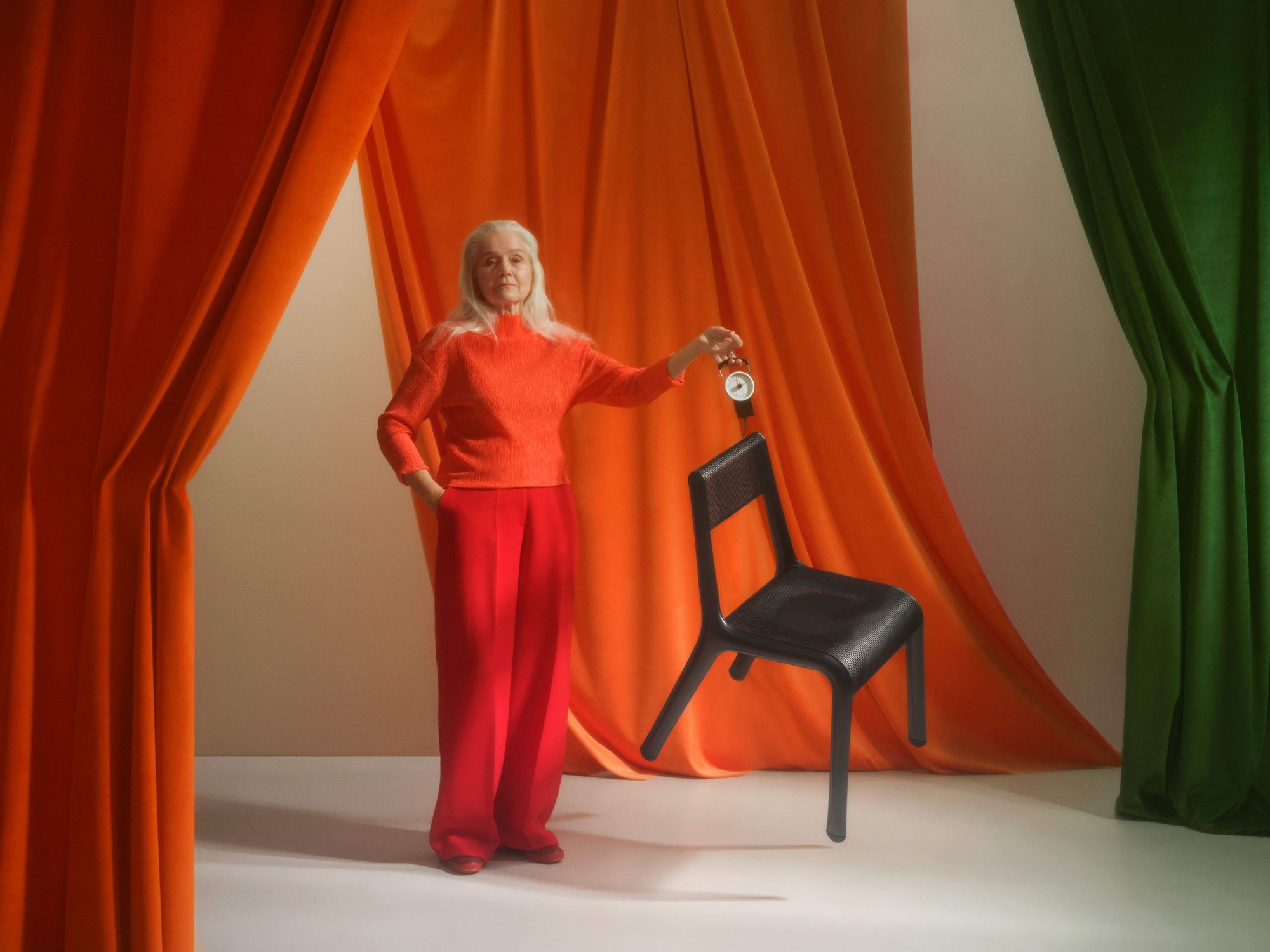
In an age where we are faced with piles of objects due to overconsumption, what do you think is the role of design and what makes an object stand out?
I would answer this with the example of the ULTRALEGGERA chair. The ULTRALEGGERA is an object that has been brought to life by the challenges of modern life. Made from a single material, aluminum, the chair follows the philosophy of single-material thinking and is therefore fully recyclable. It also meets the criteria of the circular economy. In essence, it sums up everything the studio believes is of value in design today. Its final form and proportions, and the fact that it is made from a single material, encapsulate the potential responses to contemporary issues and challenges in ecology, technology and economy.
Furthermore, how else can ZIETA Studio’s work contribute to the circular economy?
For me, from the very beginning of the development of FiDU technology, it has been important that we develop in a sustainable way and to use materials wisely. In the early days of development, our single-material furniture was less popular, but now many companies are interested in it because it is easy to recycle. For a few years now, ZIETA Studio has been incorporating some of the principles of the circular economy into its daily operations, both at the level of process-oriented design and at the level of construction. A well-designed workflow leads to smarter use of materials (e.g. steel, copper and aluminum). The lightweight of the final product helps to reduce energy consumption during transport, and by using only one material, a single trip is enough from the sheet manufacturer to the studio. Once an object reaches the end of its life cycle, it can be fully recycled and can even become a new sheet metal that, with the right preparation, can be used to make a new object. We also use cardboard packaging to reduce the amount of plastic.
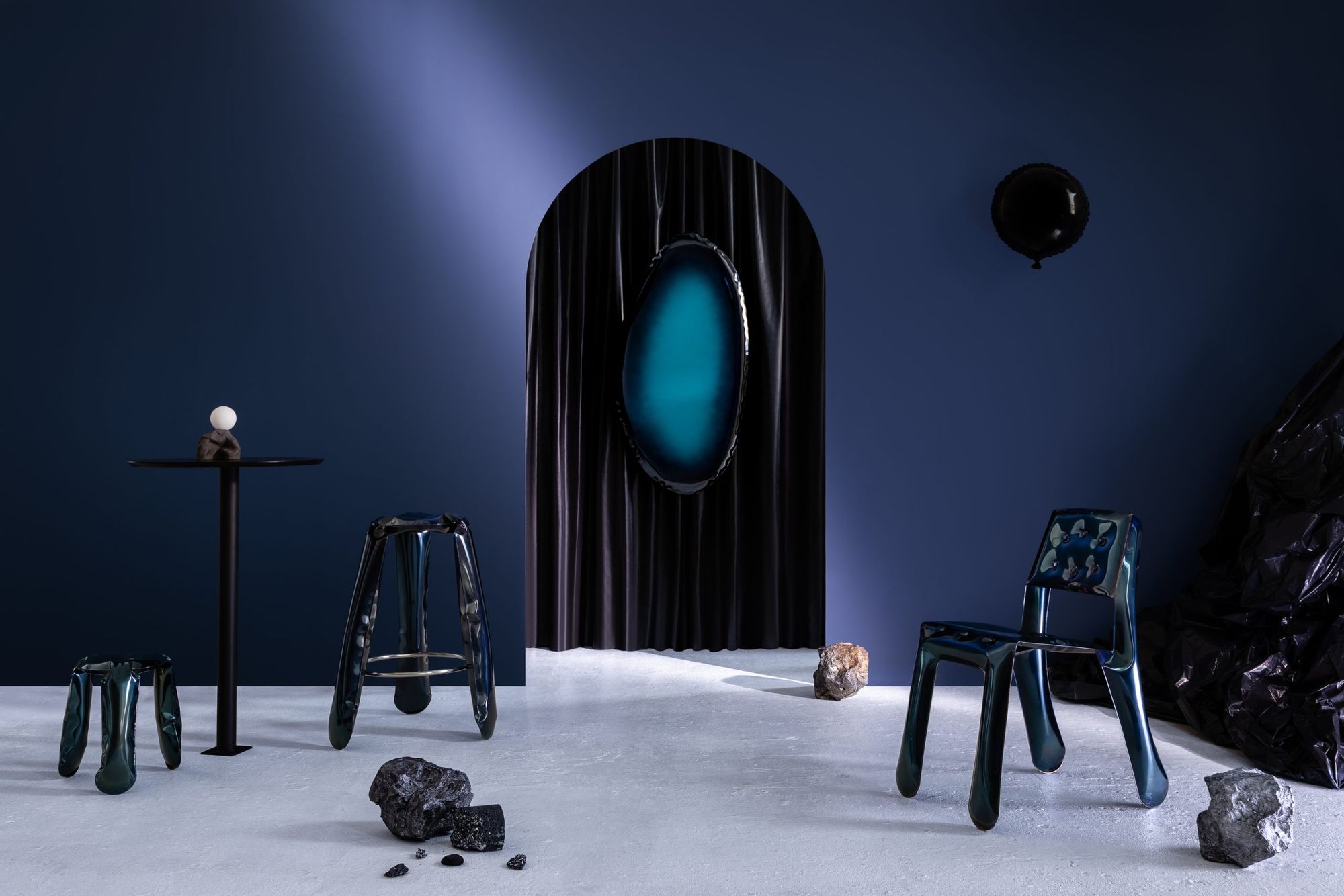
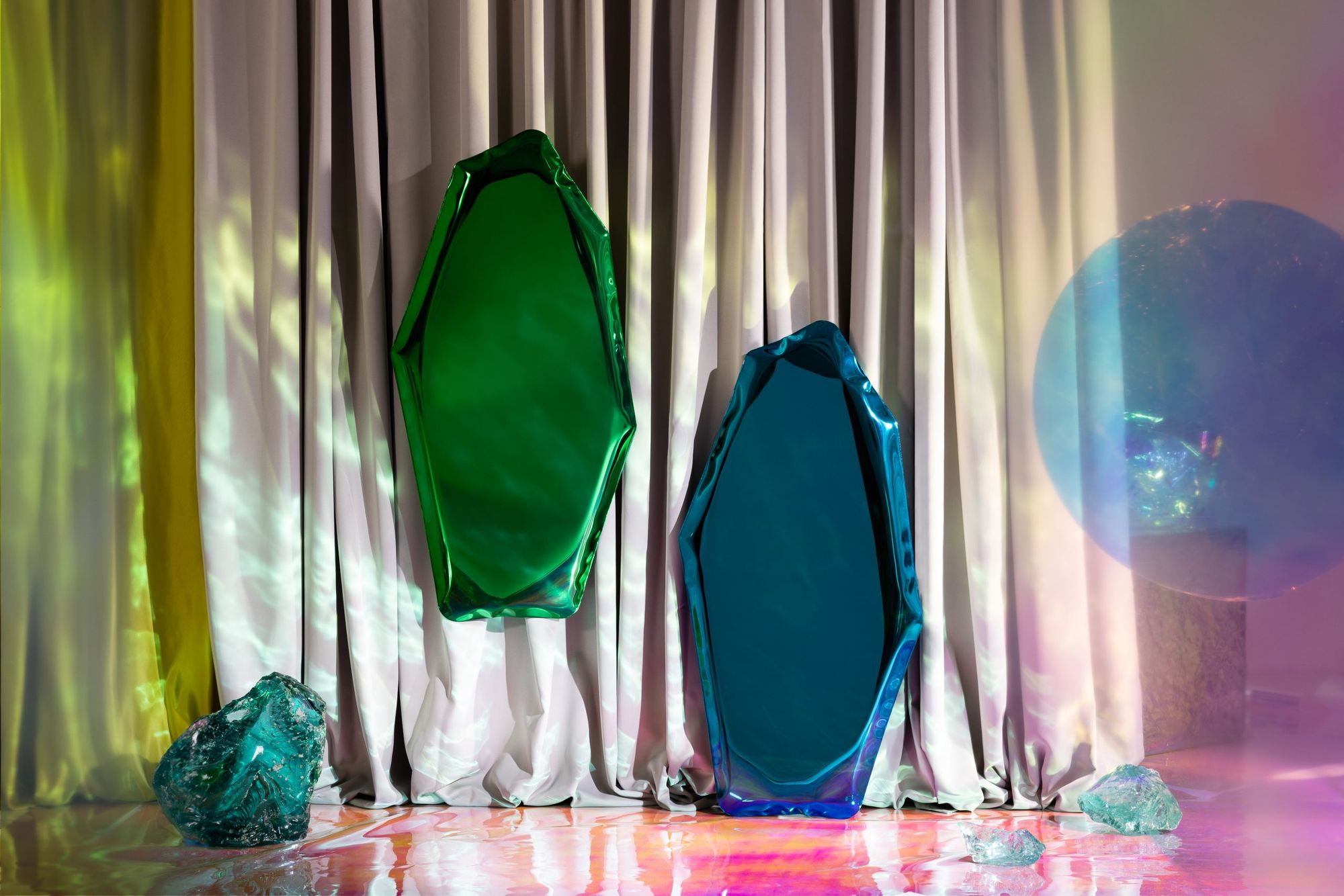
Cover photo: Laura Korzeniowska
ZIETA Studio | Web | Facebook | Instagram
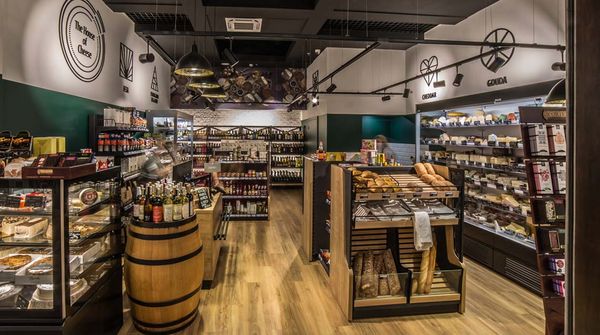
Even experts are dazzled by these special gourmet shops in Eastern Europe | TOP 5
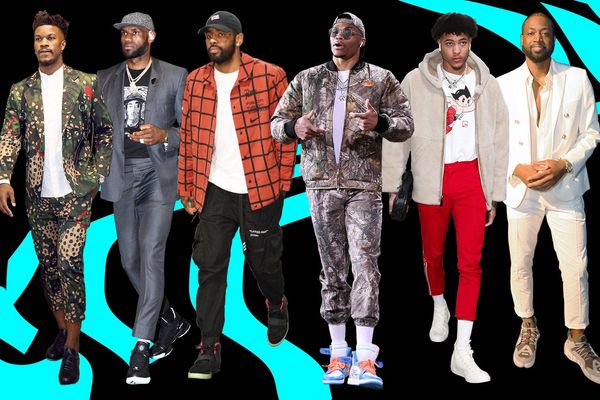
Inspiration from an unexpected source: fashion dictator NBA players
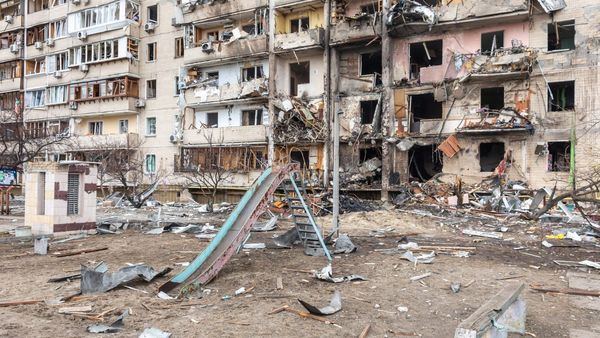