The love project born out of the sketches made during the #weeklydesignchallenge movement started on Instagram, the Slē sledge slid right up to the “Best of the Best” award of Red Dot in 2019, so that following many developments and experiments, the first prototype could be created this summer, currently waiting to be tested. We interviewed designer Ádám Miklósi.
Ádám started the development of Slē in the beginning of 2019, and ironically it is the second time that he works on designing and implementing a winter leisure tool during the warmest season. The young designer recommends Slē made out of plywood for both kids and adults. The tool breaks off with the traditional image we have about sledges. It has a sufficiently playful design, yet is characterized by a clean and high-quality look, that is generally a feature of Scandinavian furniture.
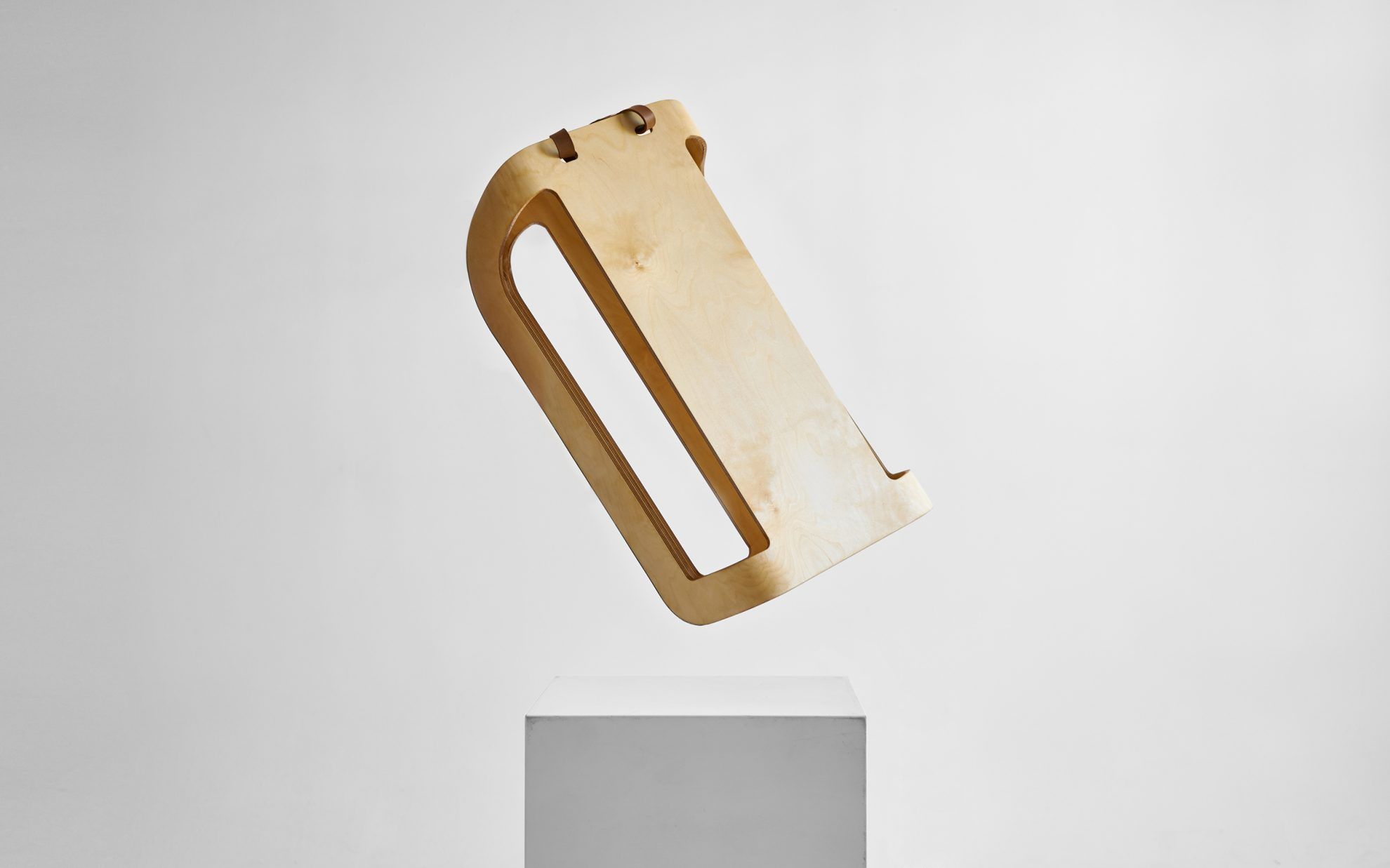
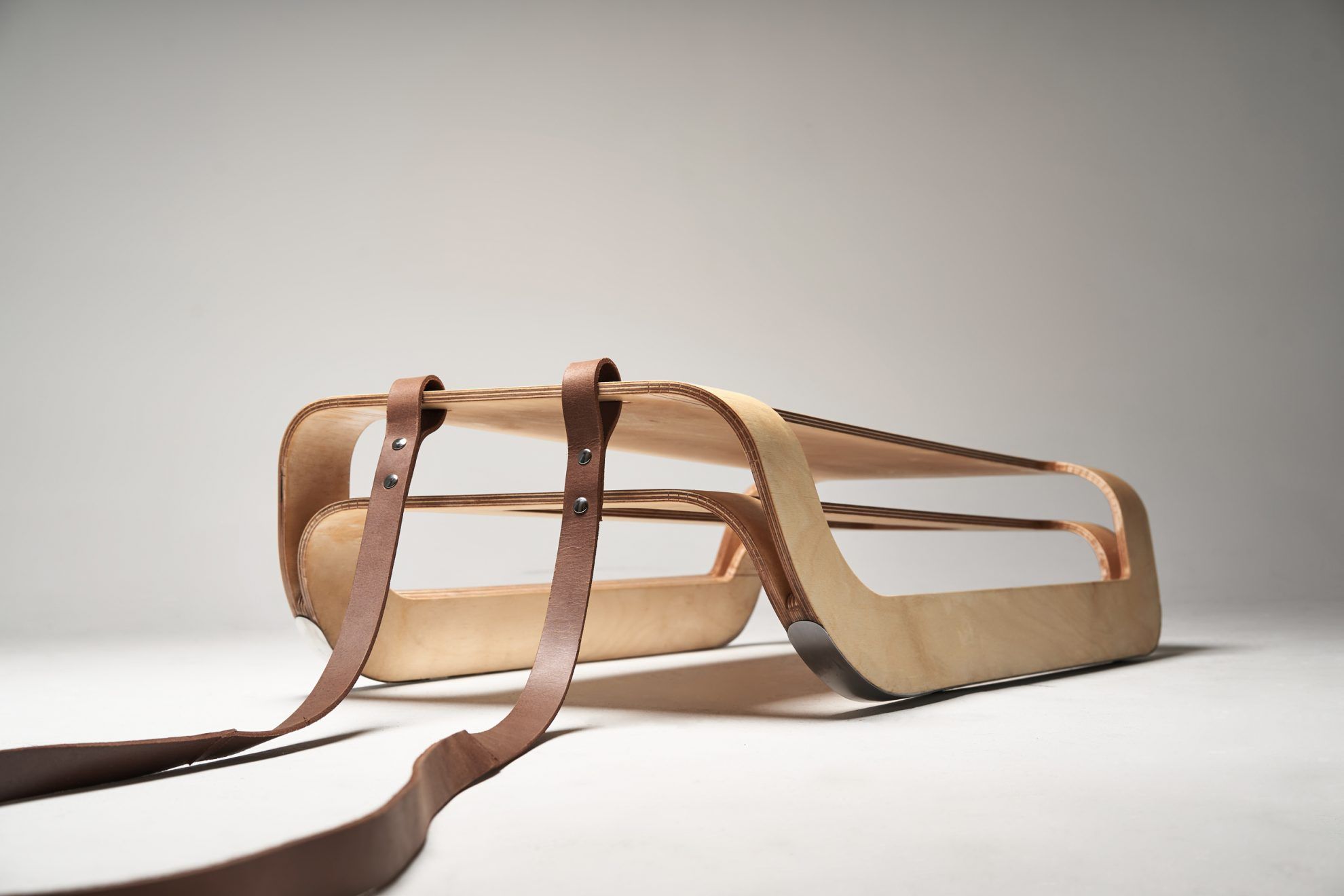
“After winning the Red Dot design award last year, I thought it was time that I continued the work. I requested many price quotations for production, but unfortunately in the case of a device of this size, manufacturing the equipment costs quite a lot, and I didn’t consider my design elaborate enough to invest into this. This is why I decided to create the first bent prototype myself” – the designer told us.
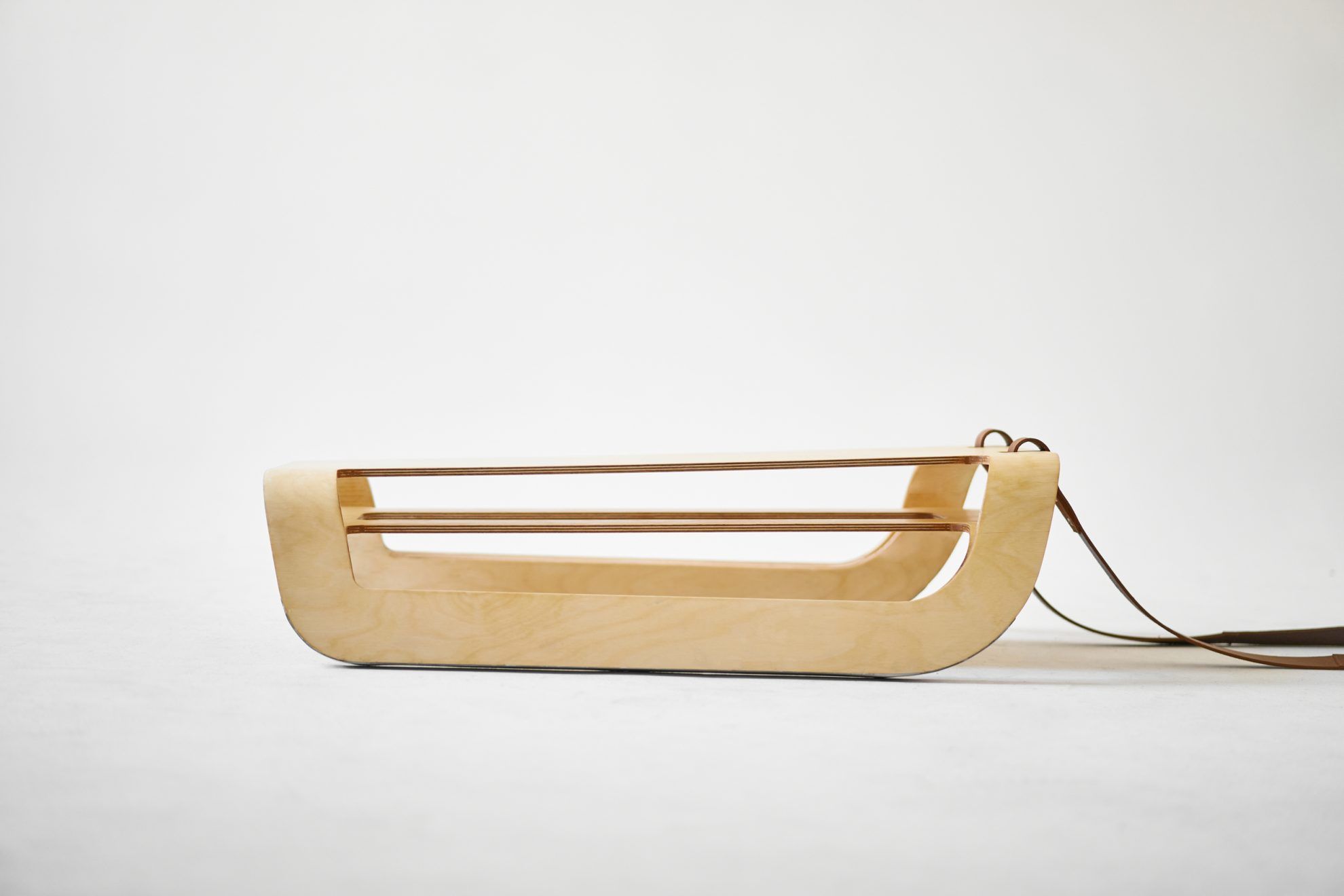
Ádám has already worked with FabLab Budapestseveral times before, they have helped his work many times. “They are a great community and on top, I live in the next street, so they were a quite natural choice to me. They had all equipment and expertise necessary for creating the prototype. We made the milling of the die cut drawing of the sledge and the so-called kerf with a CNC milling machine. Then I started to bend the plywood to the given template. After the first two unsuccessful attempts and broken pieces, finally I managed to implement it with the help of a steam cleaner” – Ádám added.
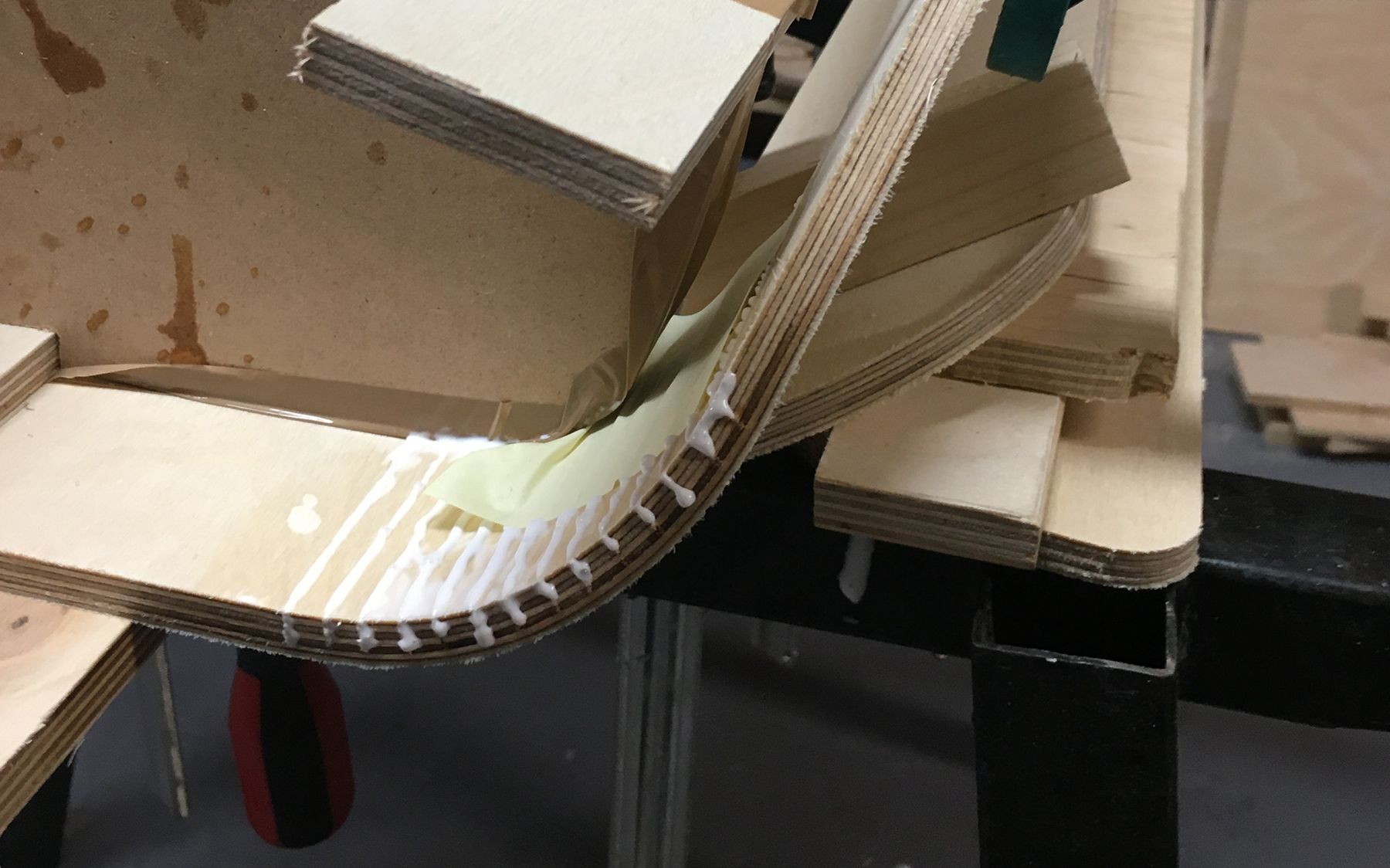
The essence of the kerf technology is that they mill grooves of a given width, depth and density out of the material to be bent, then they fill these up with glue and bend to the desired form. A great advantage of the technique is that it does not require special equipment and is quite cost-effective, however, it weakens the material significantly.
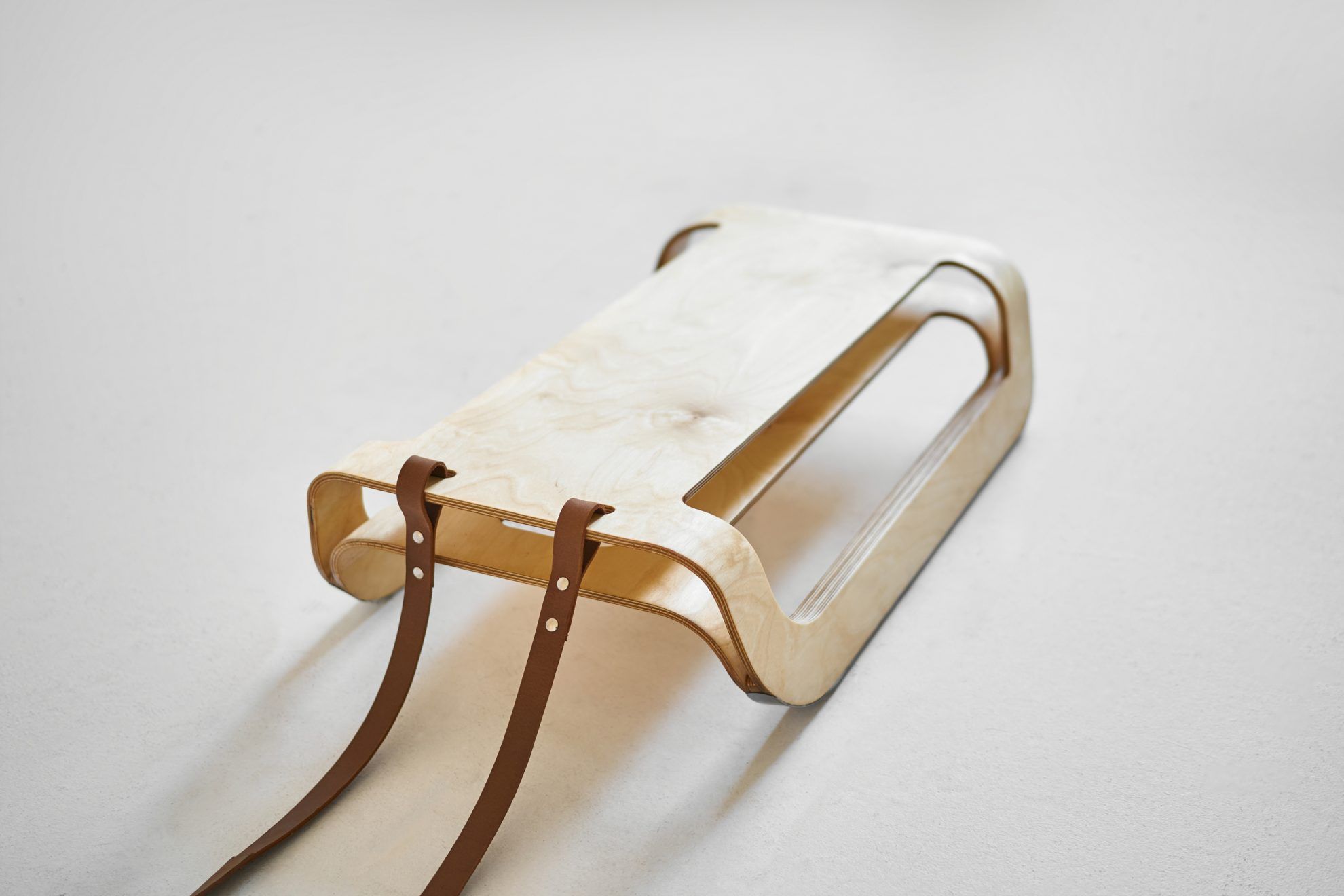
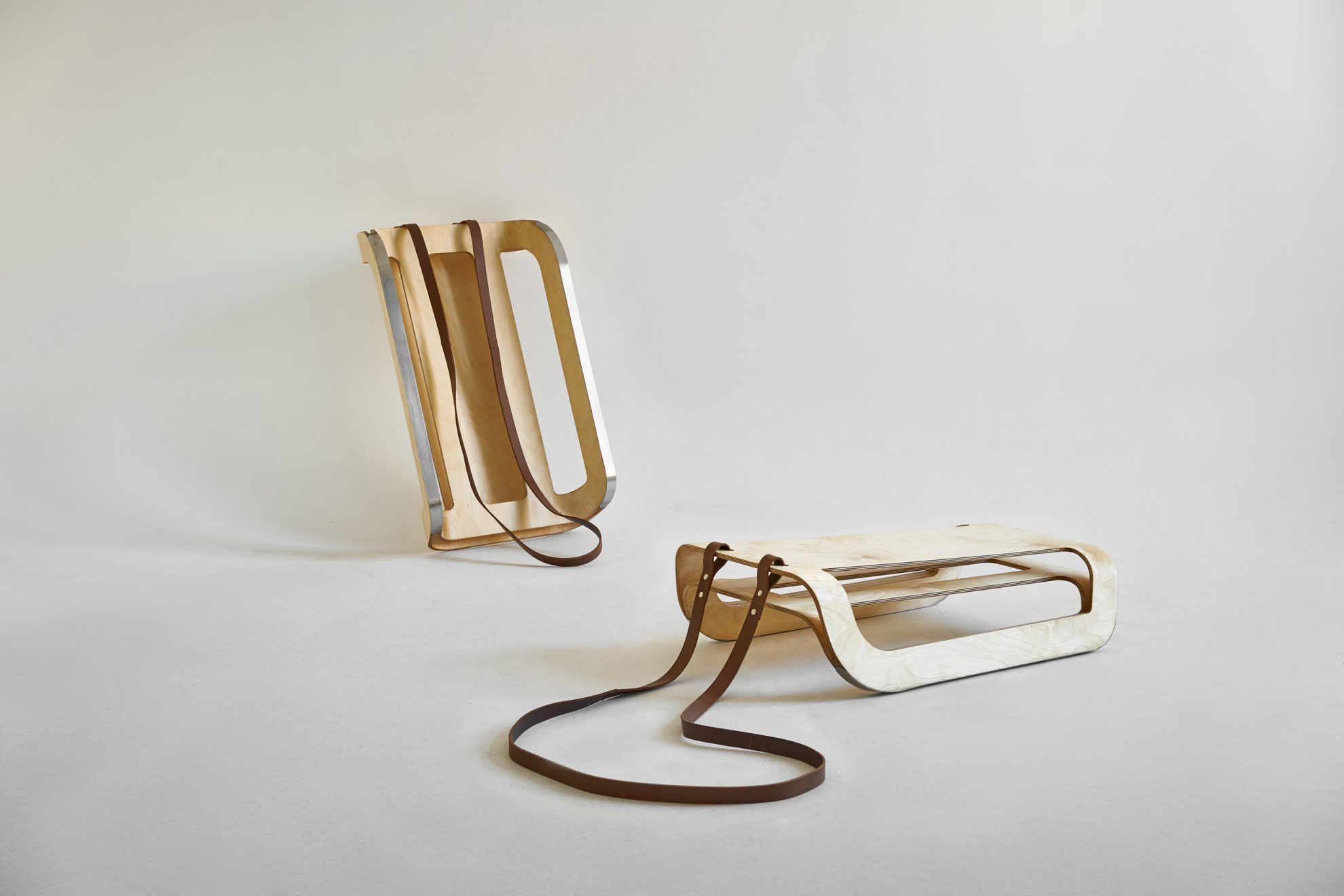
Implementing Slē took five weeks, and in addition to his other jobs, Ádám worked 1-2 days a week on it. According to the designer, he has been planning creating the prototype during the summer for a long time – for him, working in the workshop is a form of therapy. The item available for sale most probably will not be completed by next winter, however, testing could be started with a given item number. Ádám wishes to take the next steps of production thereafter. We can’t wait to see the results!
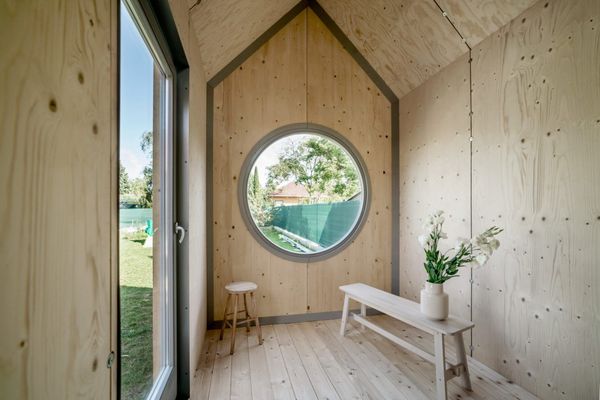
Design cabin, for an affordable price | Meet Hello Wood Kabinka!
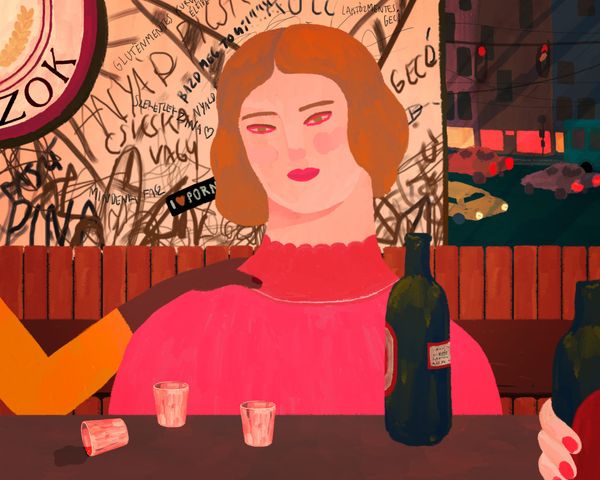
27 - My Last Day at Home | Flóra Anna Buda’s latest short film
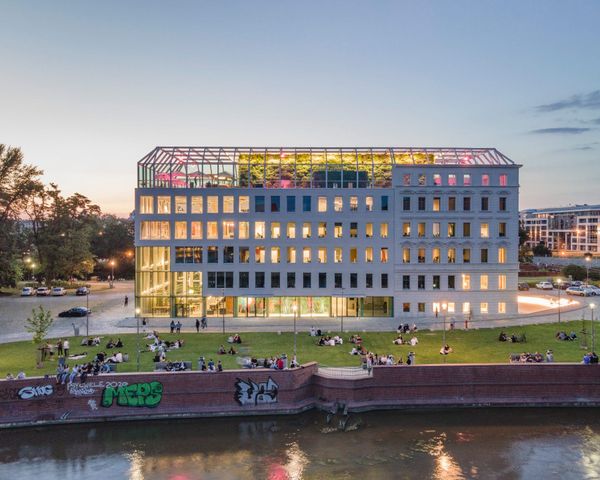