How are the comfy pieces of the NON+ brand made? What work processes does a material have to go through until it becomes a finished dress, a sweatshirt or a pair of trousers? And what do a designer and a manufacturer need in order to be able to work together smoothly? Join us for the first, introductory episode of our latest series!
Sarolta Kiss, the founder of NON+ and Emese Gaál were brought together by fate three years ago—since then, not a single day has passed without them consulting via phone, message or in person.
Over the twelve years of the brand’s existence, more than six hundred models were born: initially, the pieces were made at another sewing shop, but three years ago the manufacturing of their entire assortment moved to Emese’s. At the time, Saci was contemplating switching sewing shops—Emese and her team (PROMES ‘95. Bt.), who had already manufactured clothes for the Nanushka brand, were recommended to her by a mutual friend. By that time, they let go quite a few from the original twelve clients, and by today they have retained four permanent partners. It was a rational decision: with the less yet more reliable clients, the amount of work did not decrease, it simply became more transparent and manageable. Currently, in addition to NON+, they work with the Artista, Plié and Enemy in the wardrobe brands.
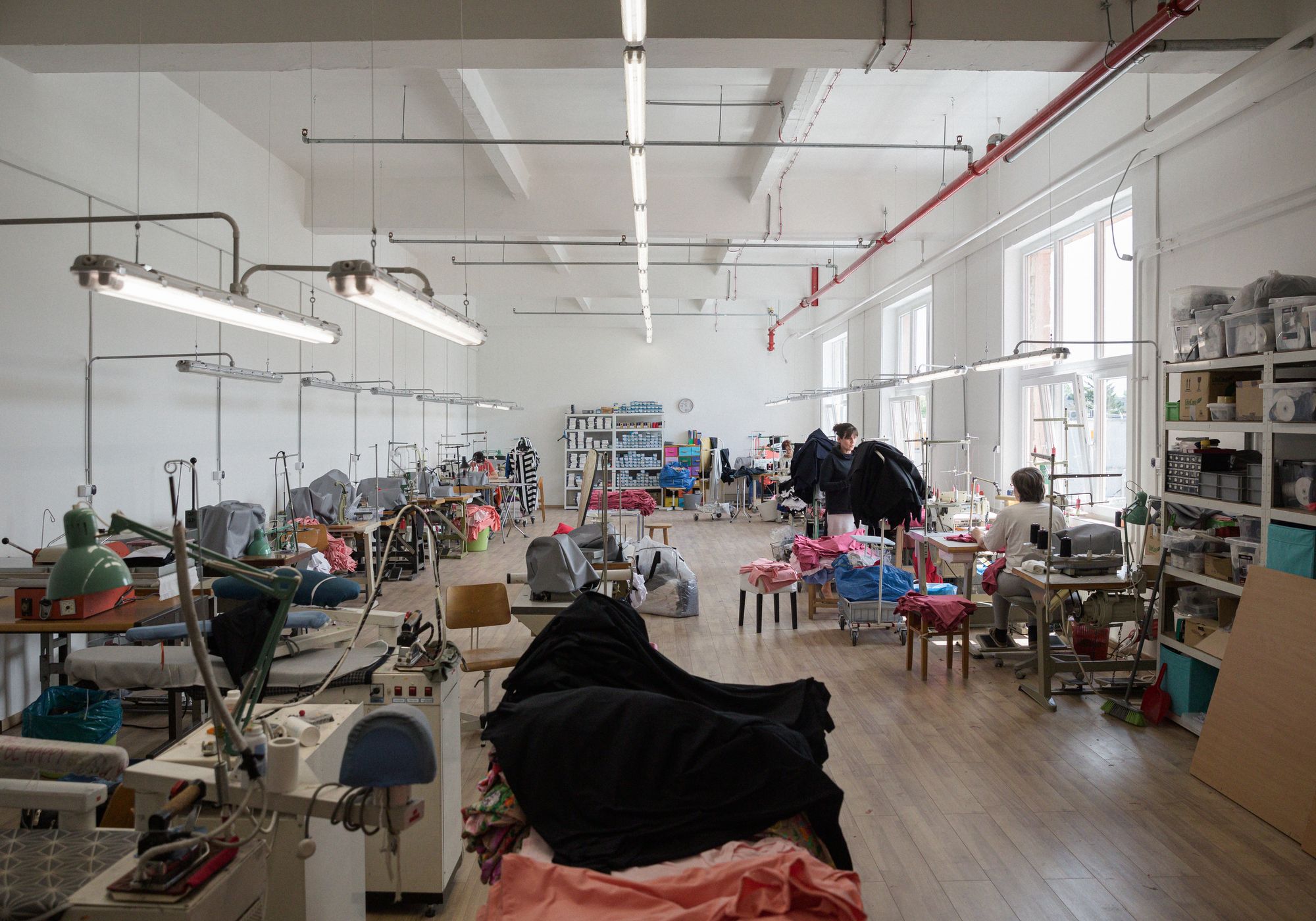
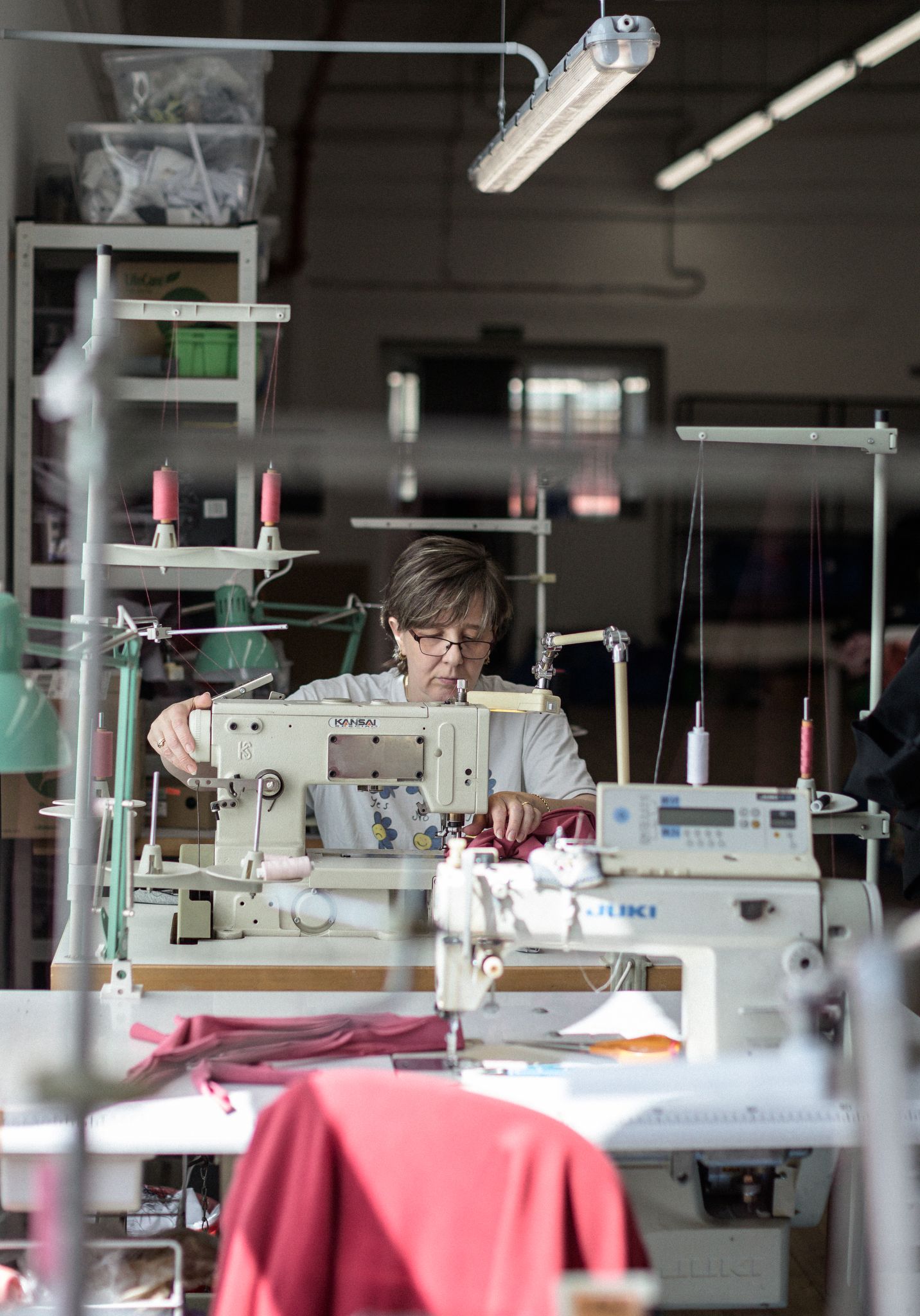
Saci and Emese meet in the sewing shop in Óbuda on a weekly basis. “We order materials and sample after planning manufacturing, and after finalization comes series production and finally packaging. I bring the drawings and ideas for manufacturing, while they think through the manufacturing methods from a professional viewpoint—we talk about all elements of the model to be made down to the tiniest detail. Everyone proposes ideas and contributes to the final look of the collection according to their best knowledge. The whole process is a teamwork,” Saci told us.
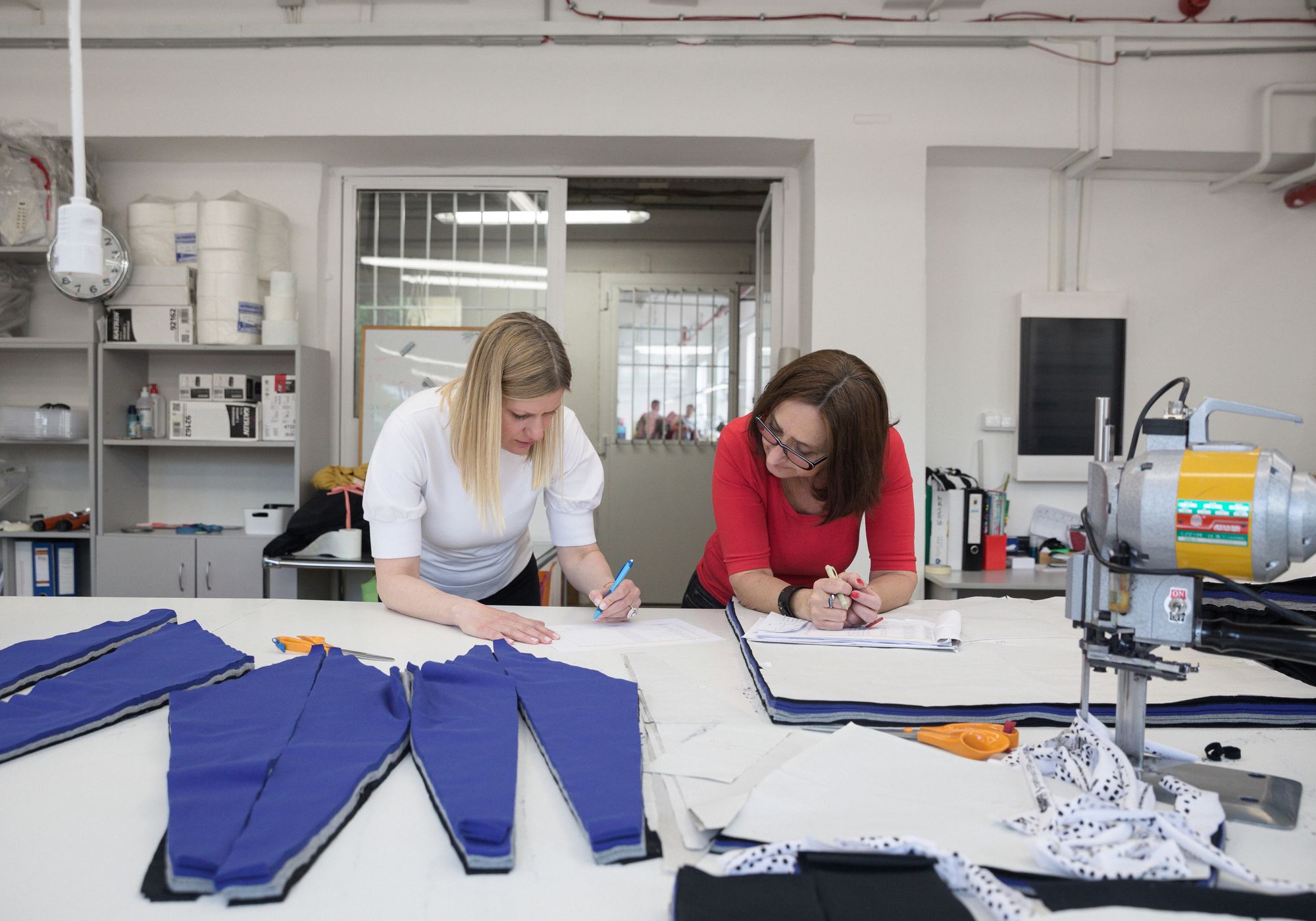
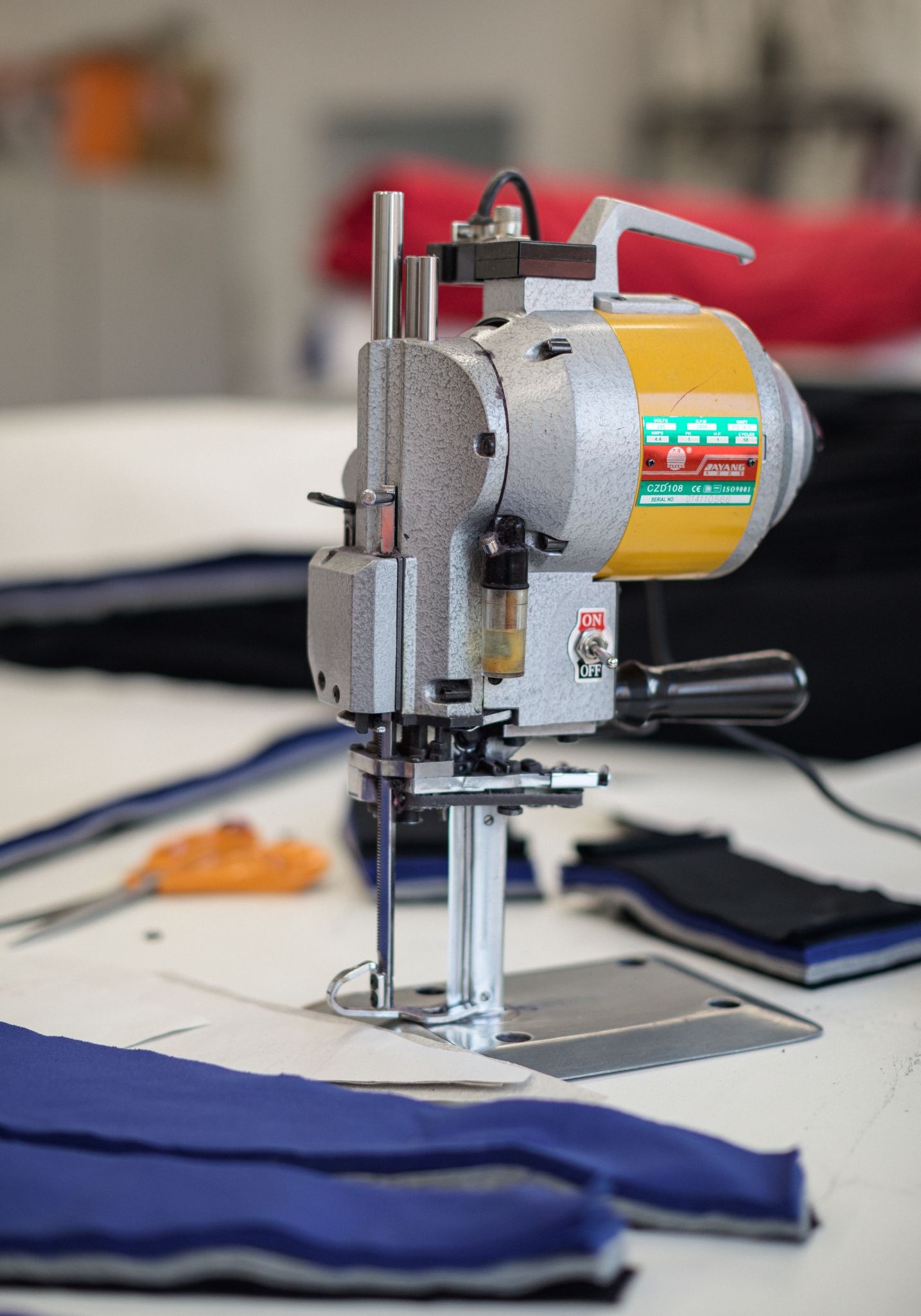
During our visit to the sewing shop, Saci consulted Enikő, the head of the tailoring department, about different designs next to the worktable. A bit further away, Zsuzsi was tailoring the BASIC models—the preceding phase is when they spread out the materials ordered from abroad in several layers, they place all elements of the sewing pattern on the material and then iron it up. Then the elements are cut out. A tailoring machine like this can cut through up to 70-80 layers at once.
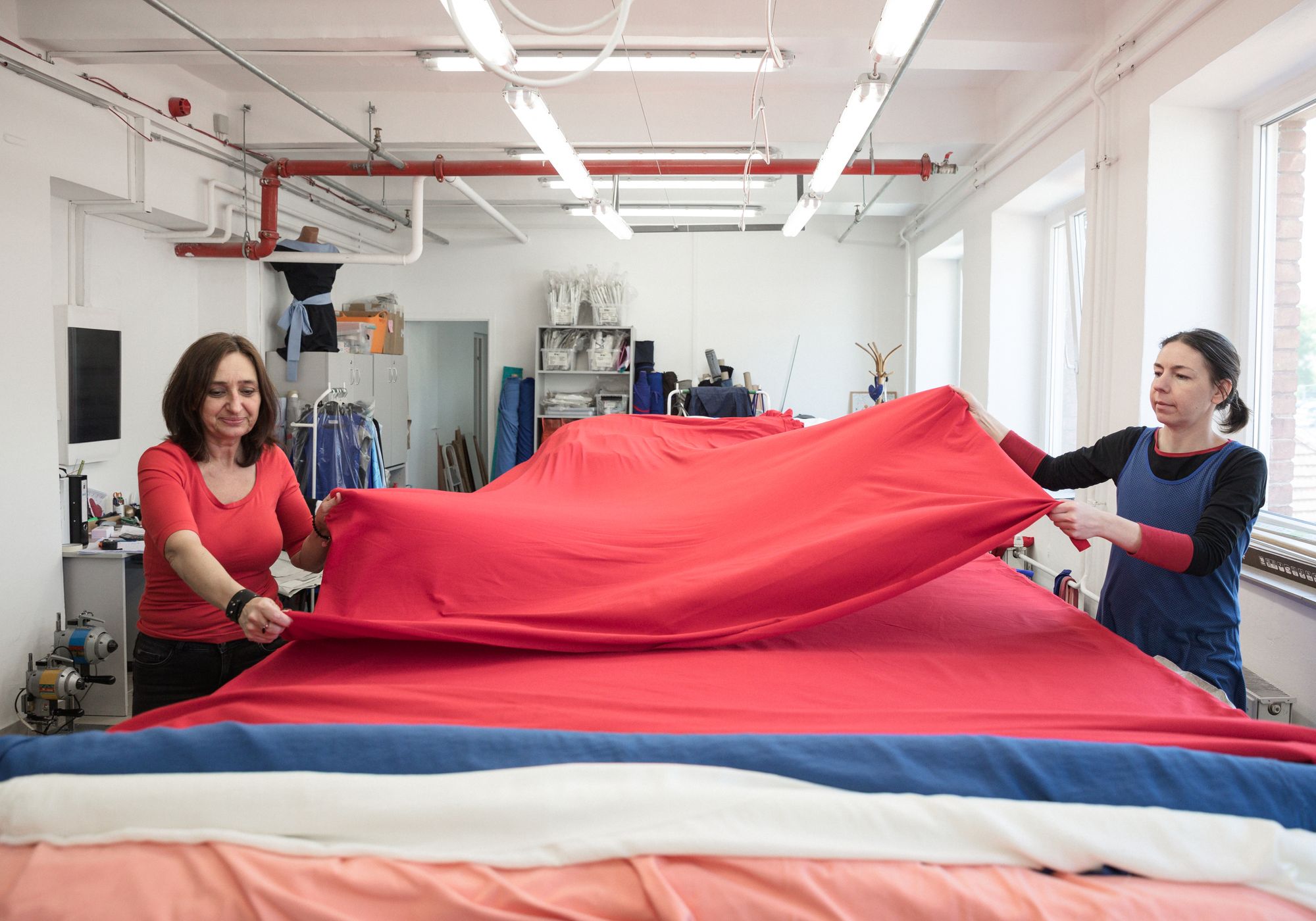
Problems can occur when the materials ordered from Italy or the Netherlands arrive faultily, for example, in a different shade or with a different width—these are all factors that influence the number of items that can be manufactured from them. There’s no use of the pattern catalog if the materials arriving to the sewing shop look differently. At another table, Erika, the modeler was working diligently. In the meantime, the small, pink “Barbie iron”, as the workers here like to call it, also popped up.
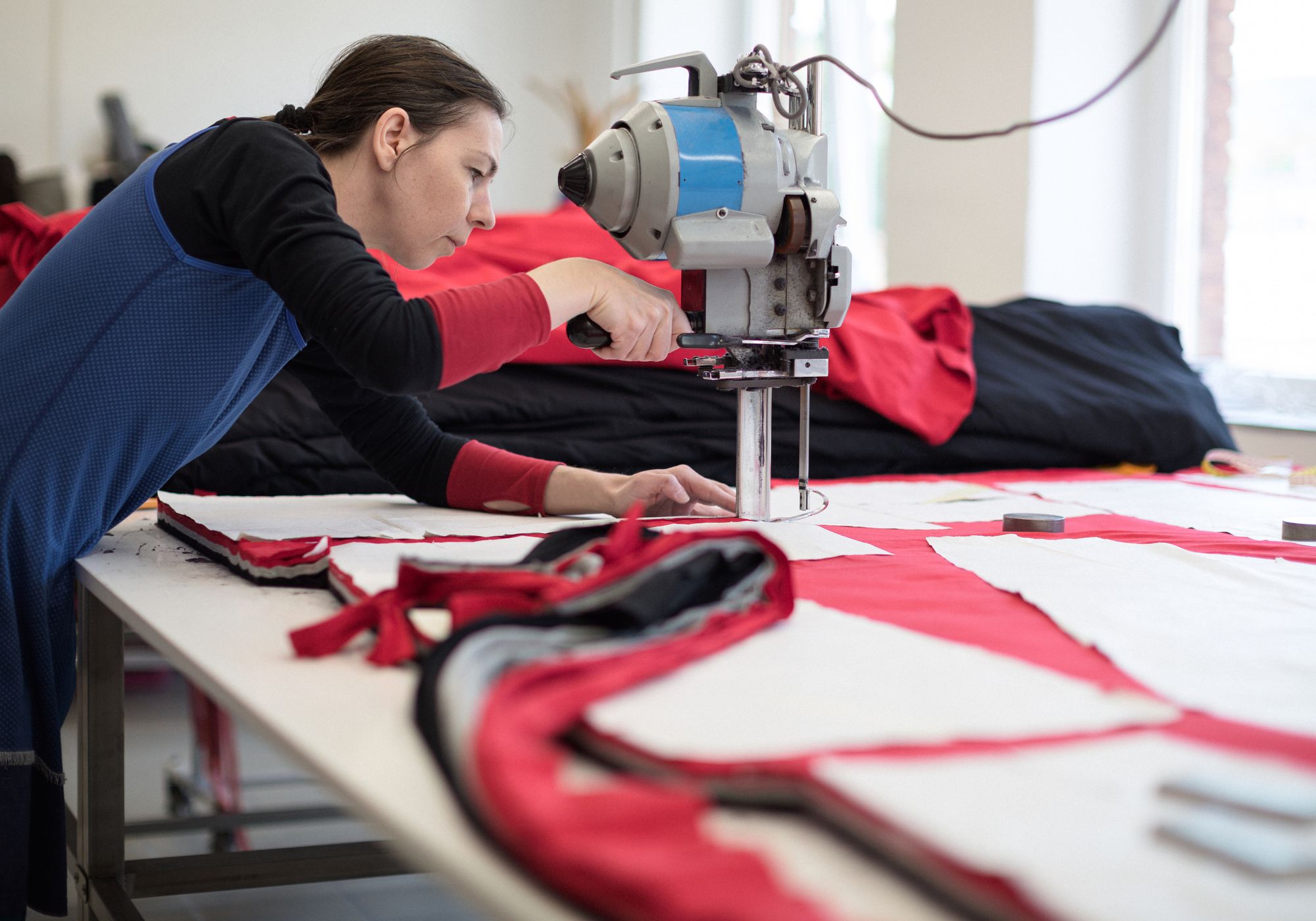
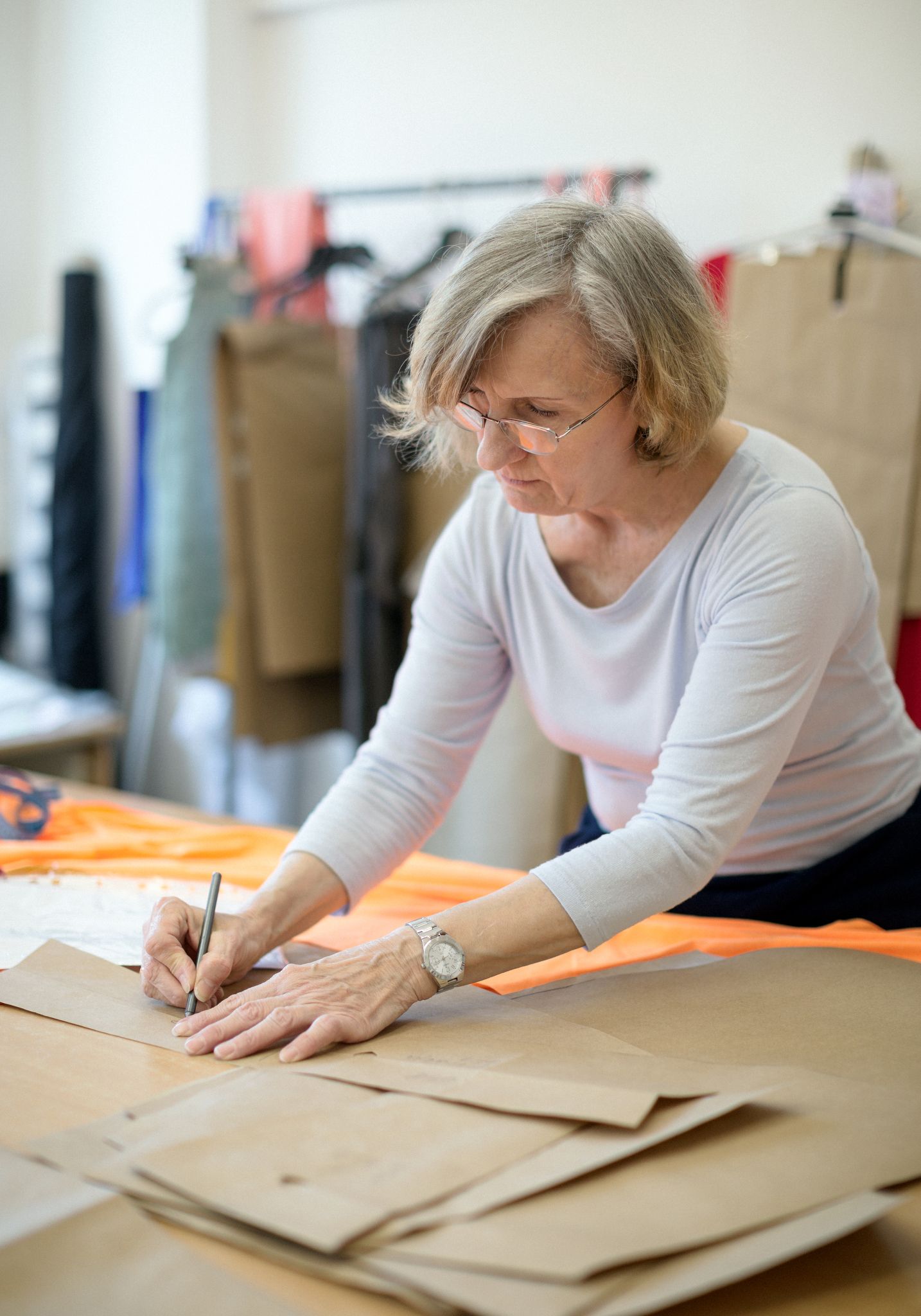
Emese and her team moved their sewing shop to a new place just a few days before our arrival: their new headquarters in Budapest’s District 3 can accommodate everyone and everything comfortably. Even though not all elements have found their final place yet, the tailoring and sewing machines are working relentlessly, and all workers are doing their jobs quite naturally.
Not only the employees, but Emese, the owner of the sewing shop, too, who monitors all work processes and in the meantime she does paperwork, organizes, consults the accountant in her half-furnished office and manages all operations concerning the sewing shop’s life. She considers herself a maniac, who doesn’t stop for a minute: she delivers materials to the seamstresses working from home, too, if need be. There are twenty people working in the sewing shop at the moment: the majority of workers are women, the male sex is represented by János and Józsi. Most of the team is from Budapest, but there are workers from Sashalom, Ócsa, Pestszentlőrinc and Pesthidegkút, too, and there are some who work from home with their own apparatus.
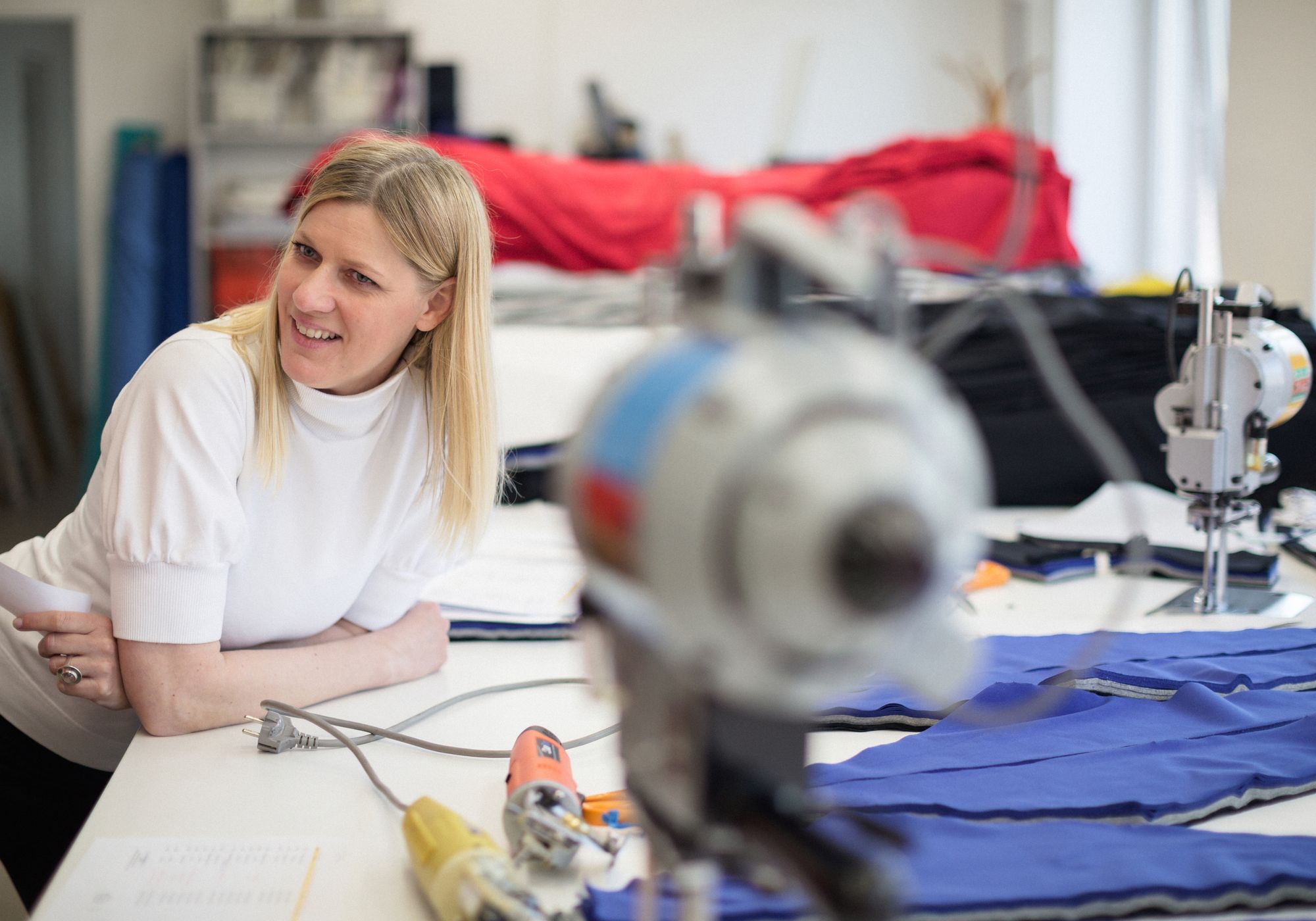
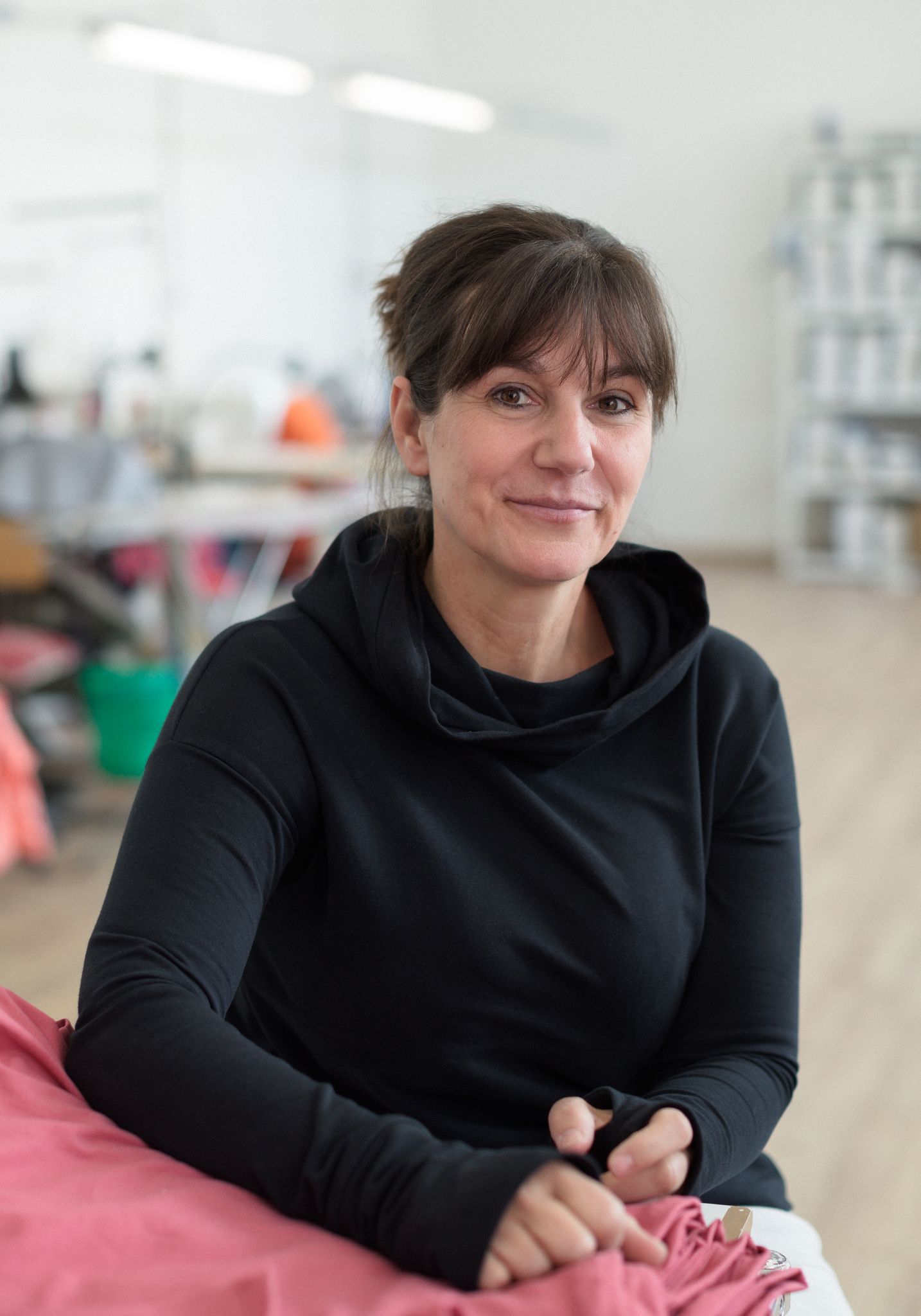
To understand their exact operation, we turned to Saci:
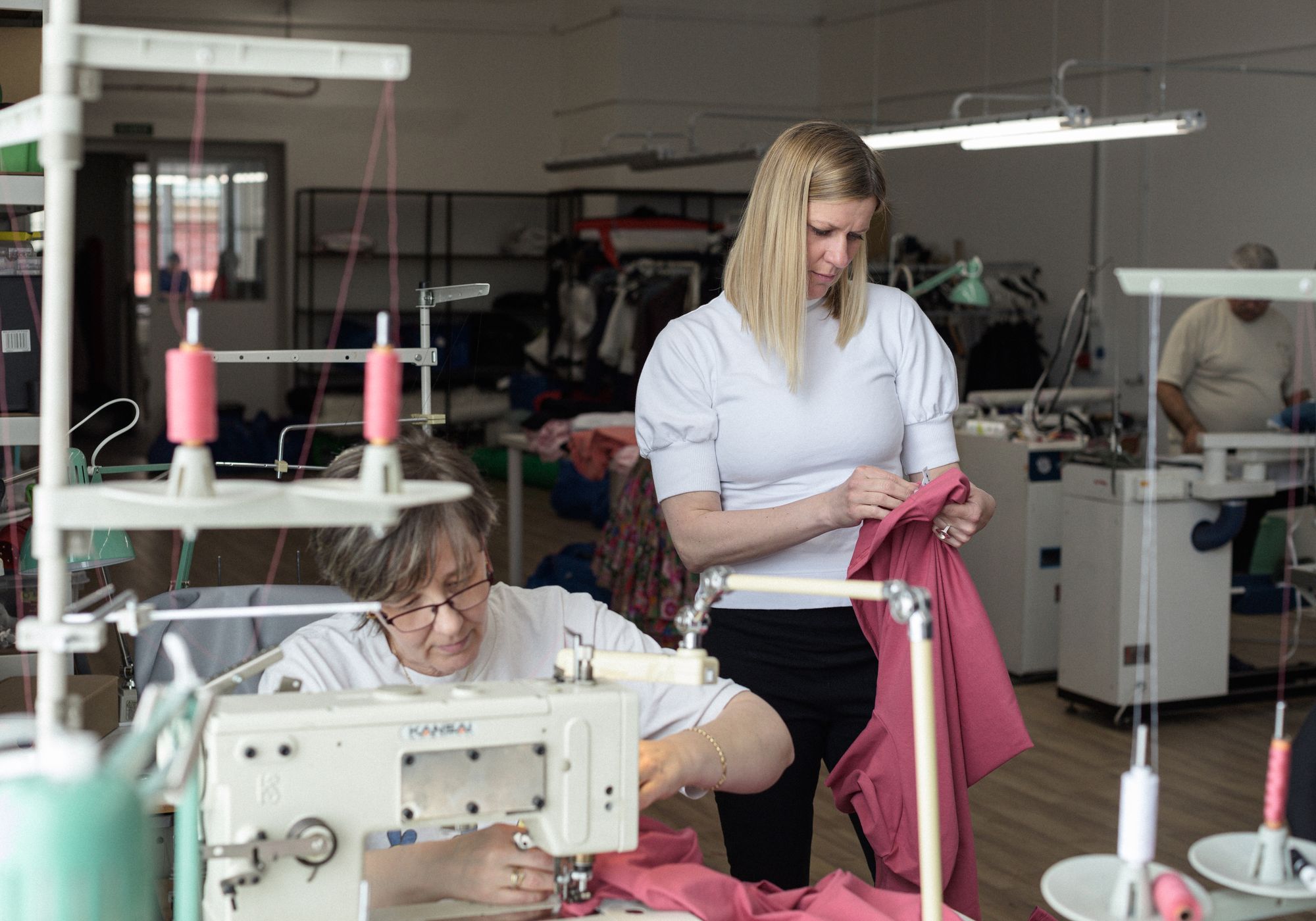
“Currently we work according to a pre-planned annual plan scheduled and broken down to the day. This contains the release date of collections, which determines the date of material ordering, then the detailed course of production, from the procurement of accessories to the date of the photo shoot, and even the tiniest details of communication and logistics. We have to coordinate a thousand tiny lines, and the NON+ team and the sewing shop has to work closely together in order for everything to be completed on time. The manufacturing quantities change by collections. We manufacture for both Hungarian and foreign markets. There is some overlapping, but we are continuously monitoring the needs of the market and we ty to compare it to NON+ principles and plan accordingly. The quantity increases every year in parallel with the number of NON+ models—currently there are thousands of items in stock, which decreases by the day, and then Emese and her team manufacture it once again in accordance with the manufacturing plan.”
Here, at their new premises, they created a separate room for NON+, where the completed, ironed pieces are packaged and prepared, and here are the more than six hundred NON+ sewing patterns and sample pieces that have been made since the brand’s launch in 2018. The clothes are packaged by Melinda, who also updates the inventory and sorts the packs by their destination: part of them are delivered to the NON+ showroom, another pack goes to the logistics partner and there are some intended for sales abroad.
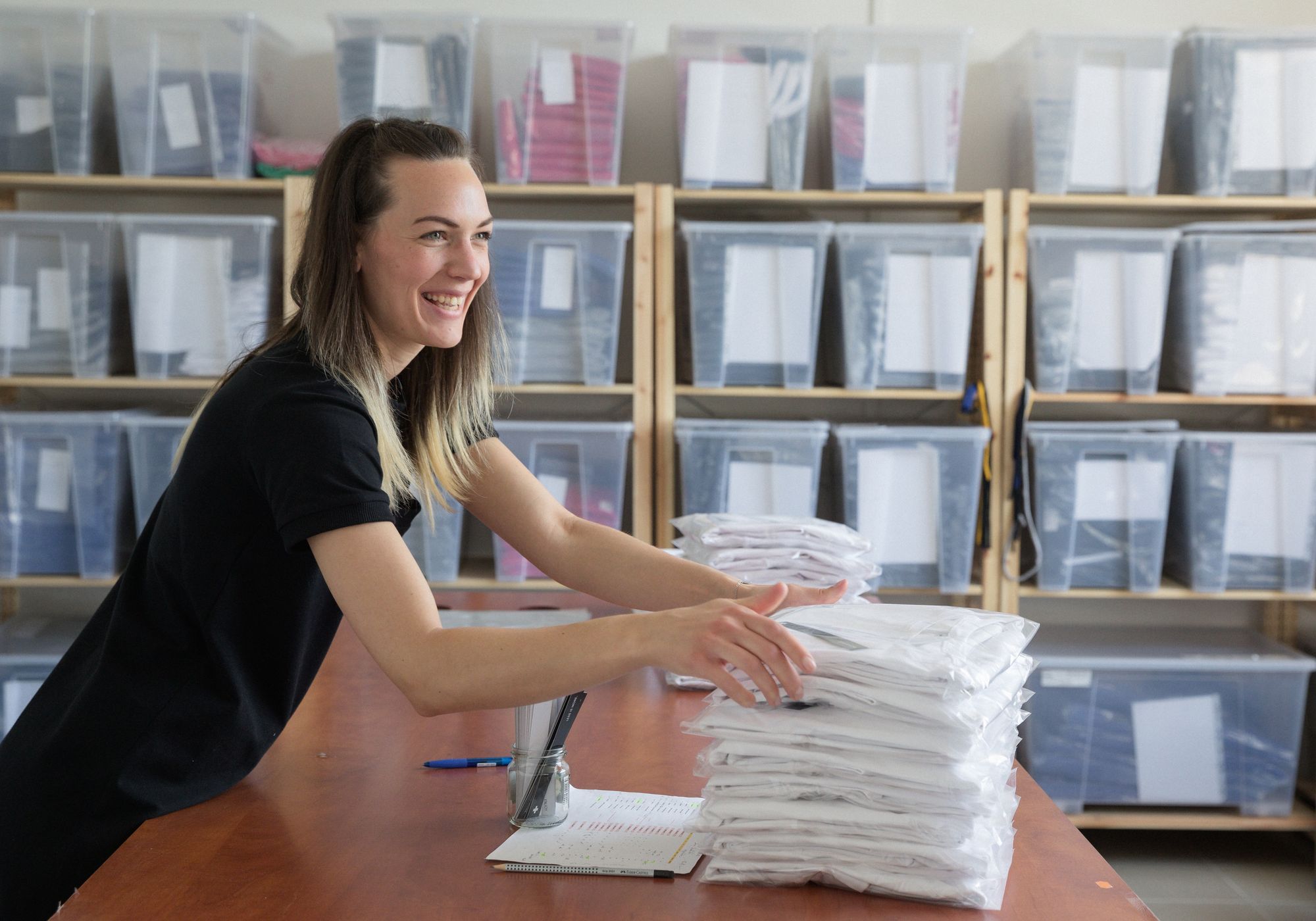
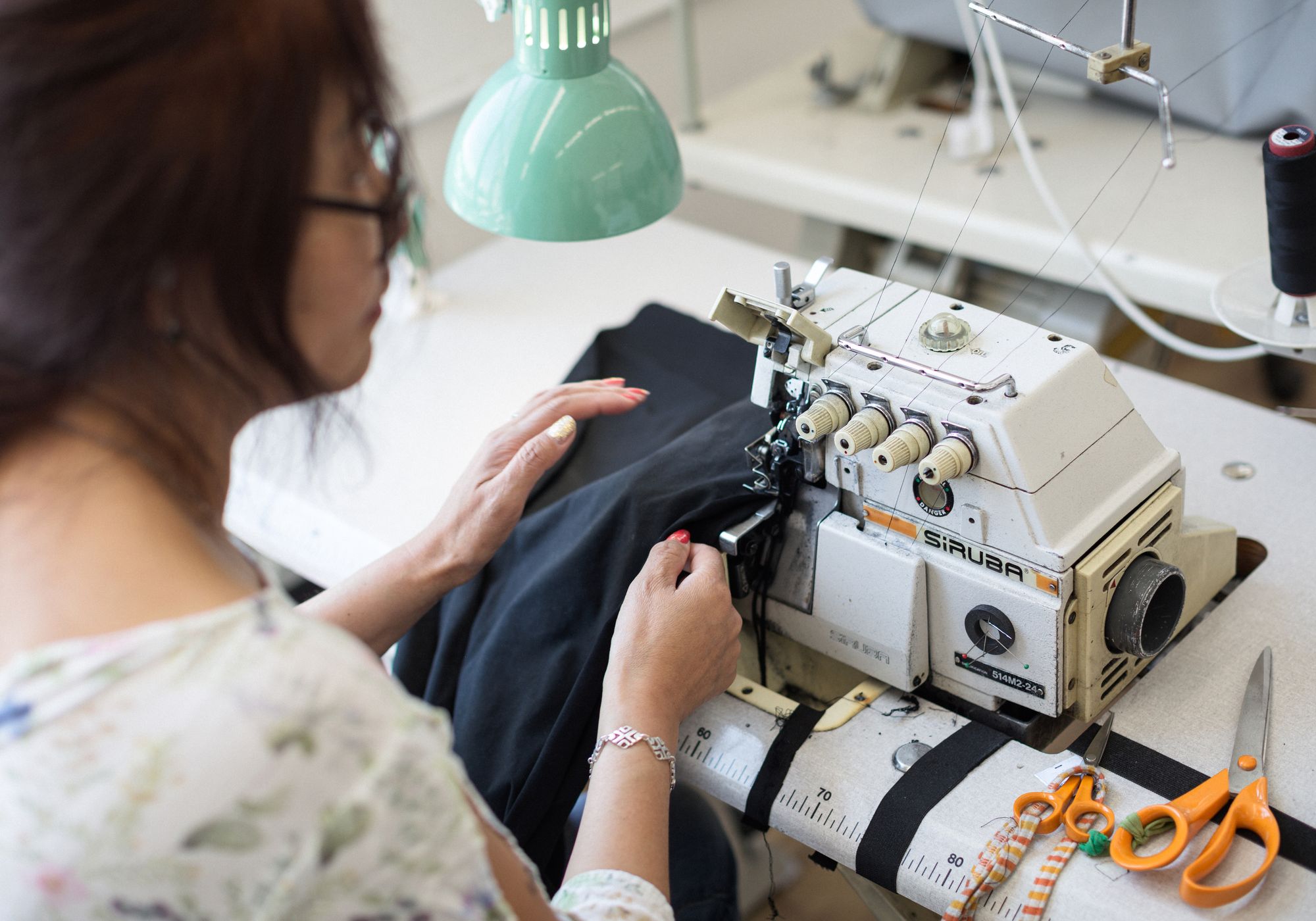
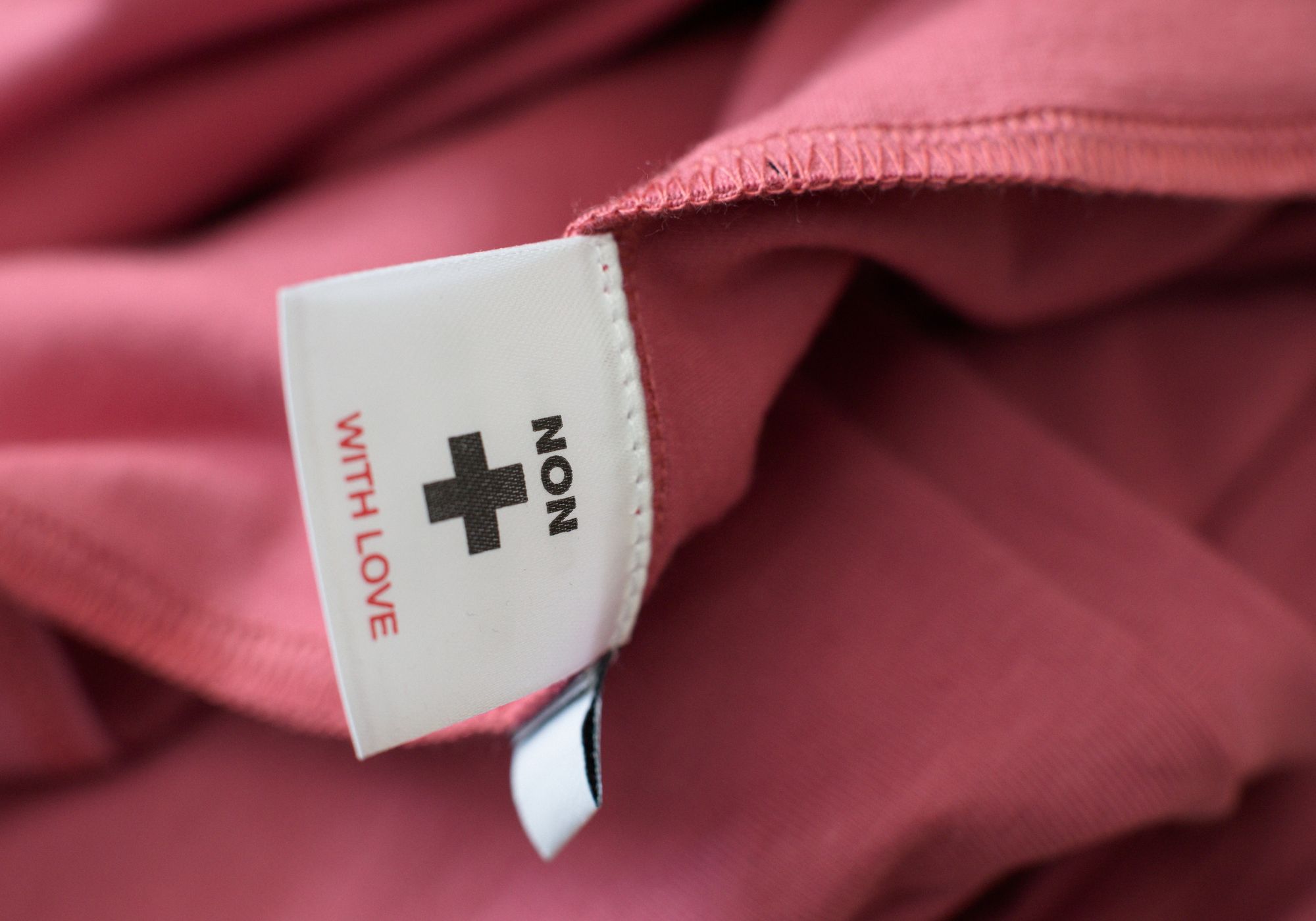
“Respect, patience, helping each other’s work and striving for continuous development are all inevitable parts of the work together,” Saci told us. This loyalty, empathy and professional humility are almost palpable—not only Saci and Emese, but all workers of the sewing shop get along well here. This is not an impersonal factory where they focus on quantity and work next to a production line: here everyone has their own work station and everyone has enough space and time. Even though they have dedicated working hours, Emese handles individual needs flexibly. Józsi, for example, explicitly asked that he could start work as early as possible: he is here at five in the morning every day and starts ironing. Enikő usually starts at nine in the morning, but stays longer: she can consult Emese about the various tasks around five in the afternoon, when the shop is more quiet, the most effectively.
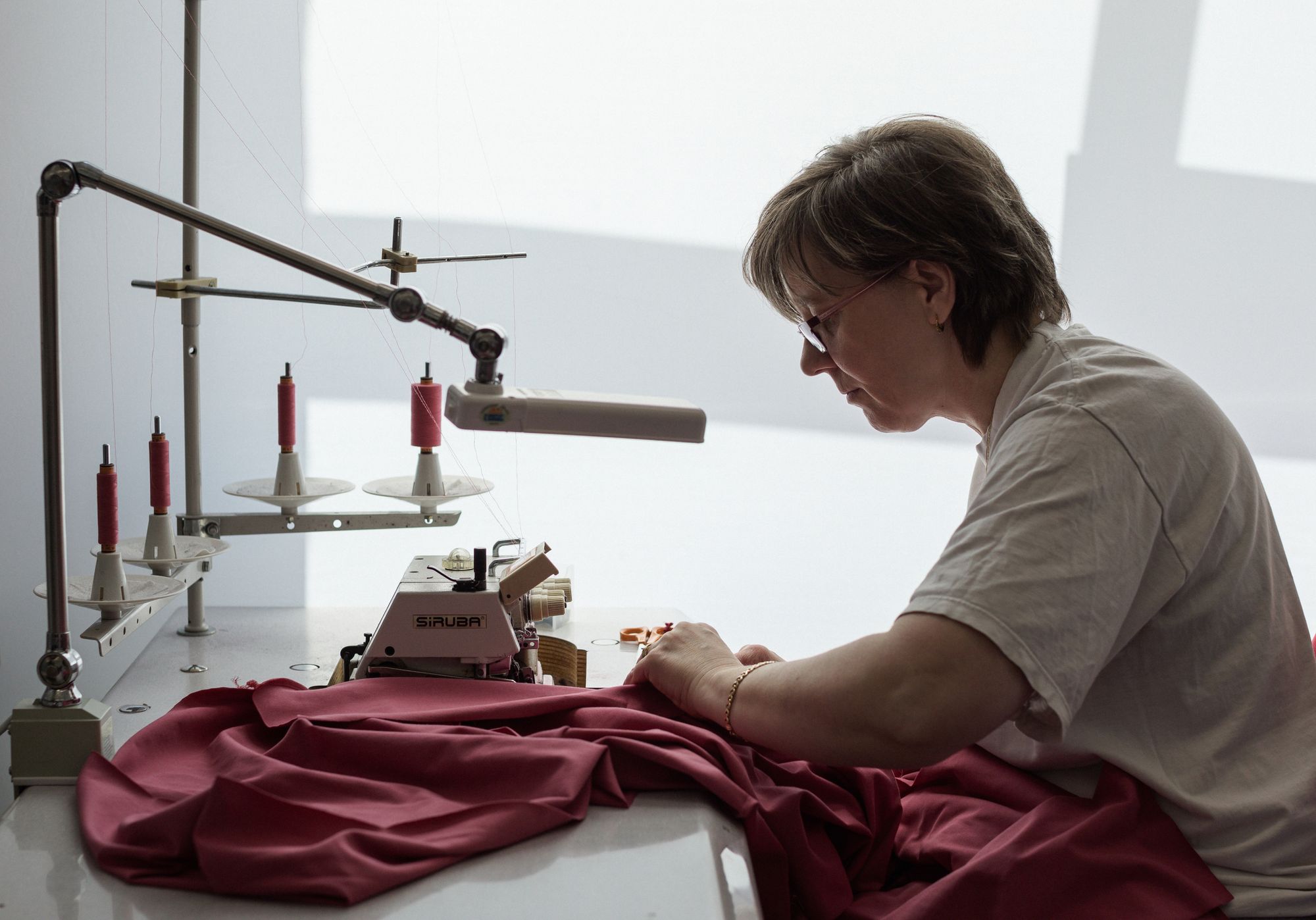
Running a sewing shop is a huge responsibility. Quite many sewing shops were shut down because they only served a single client, and such a workplace can easily become vulnerable in a critical situation in the market: this is exactly why they have less yet more conscientious partners.
Emese pays special attention to make sure that every worker feels appreciated—they hike together and celebrate birthdays and name days, too. They visited NON+’s new showroom together, where the colleagues posed in front of the mirror proudly with their favorite items (the one they like the most or the one they made themselves). “NON+ is very stylish and consistent. I keep seeing their pieces on people in the streets, in the store or on the terrace of cafes —this is a success for me, too,” Emese shared with us.
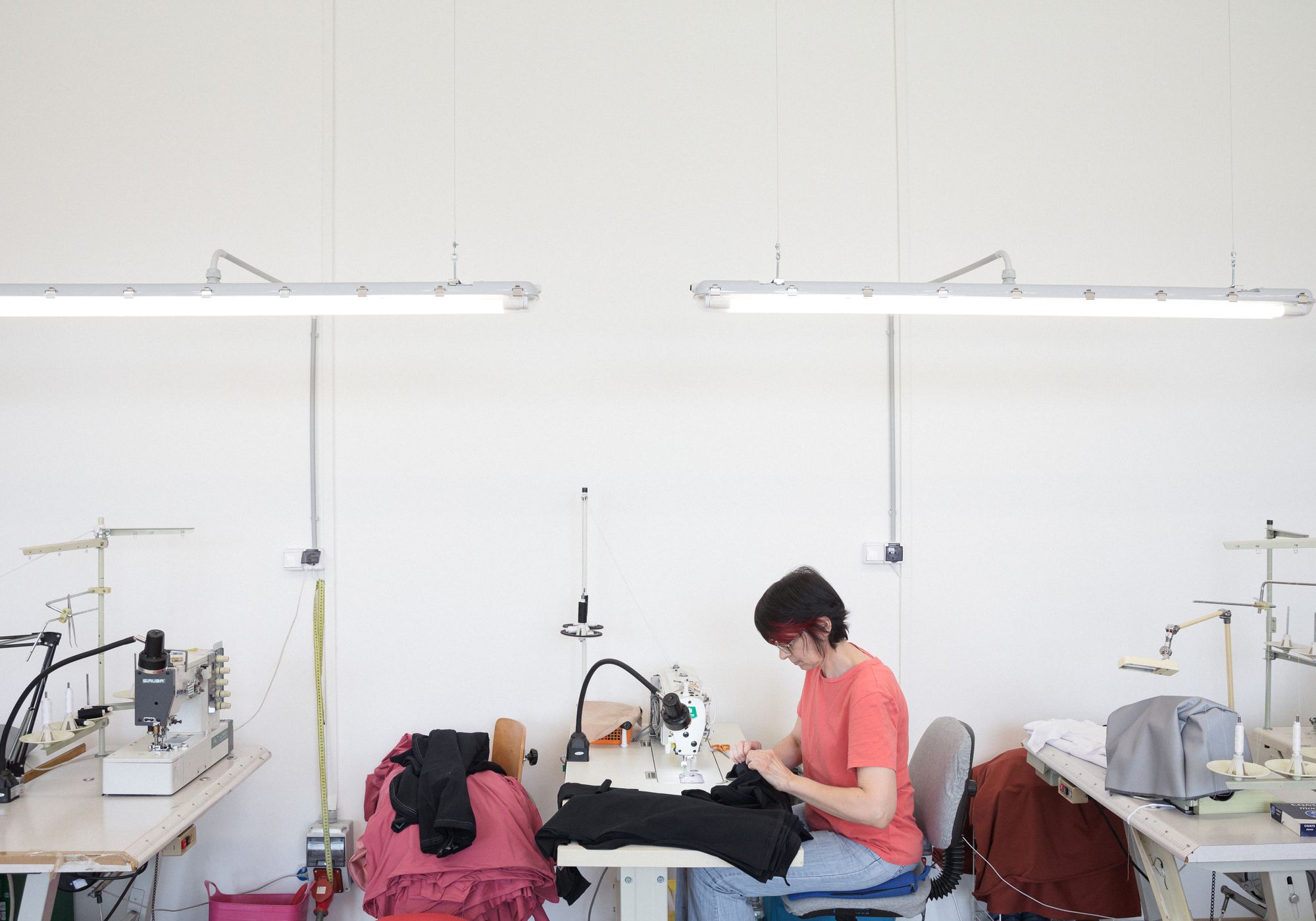
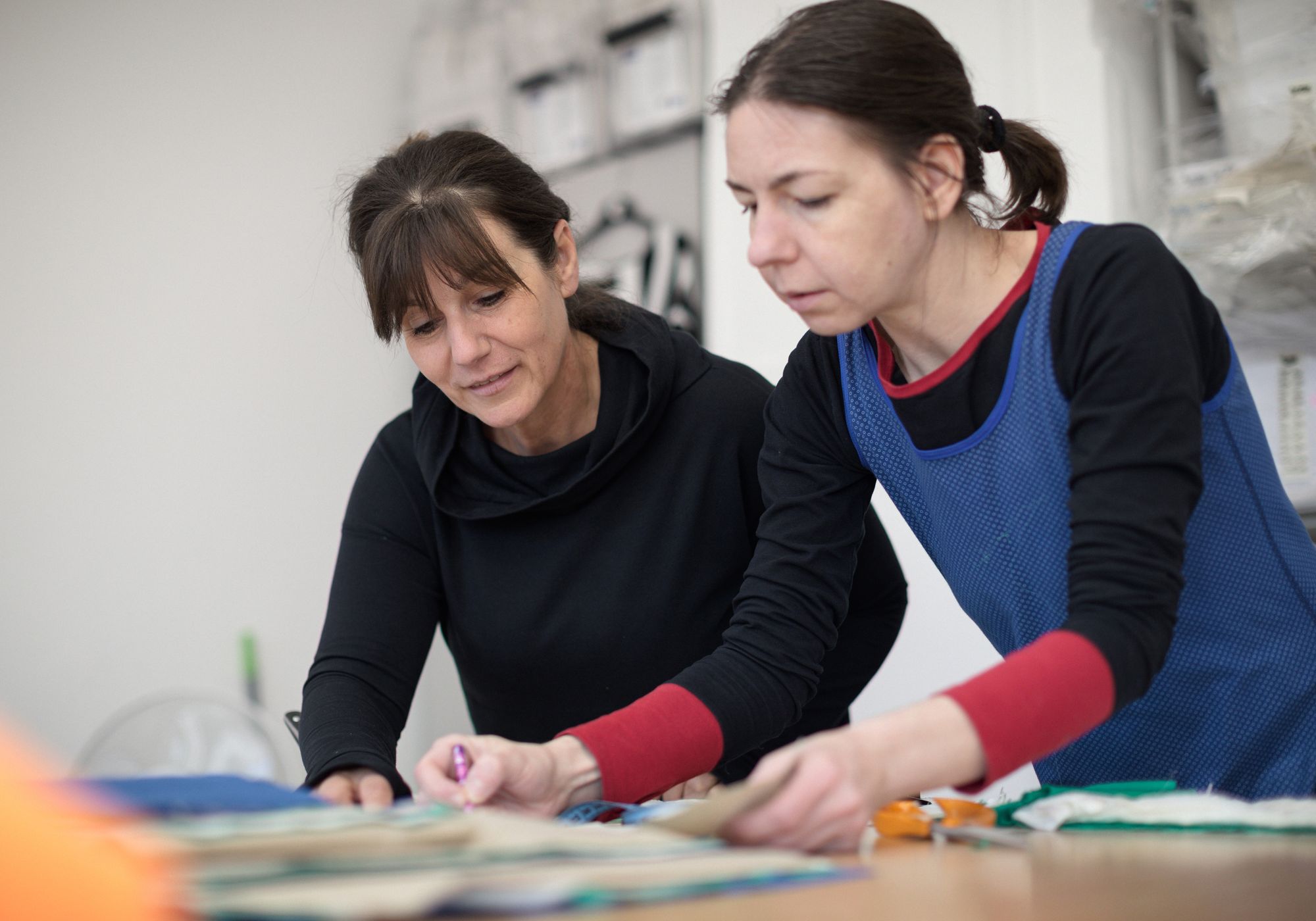
In Emese’s sewing shop, all workers know the number of the NON+ clothes by heart: they are familiar with the entire assortment, to the last thread. When we asked them which NON+ model was their favorite, they didn’t need much time to think. Enikő prefers the more formal, fitted pieces, while Emese adores everything loose-fitted and asymmetric—the NON220 model is her absolute favorite.
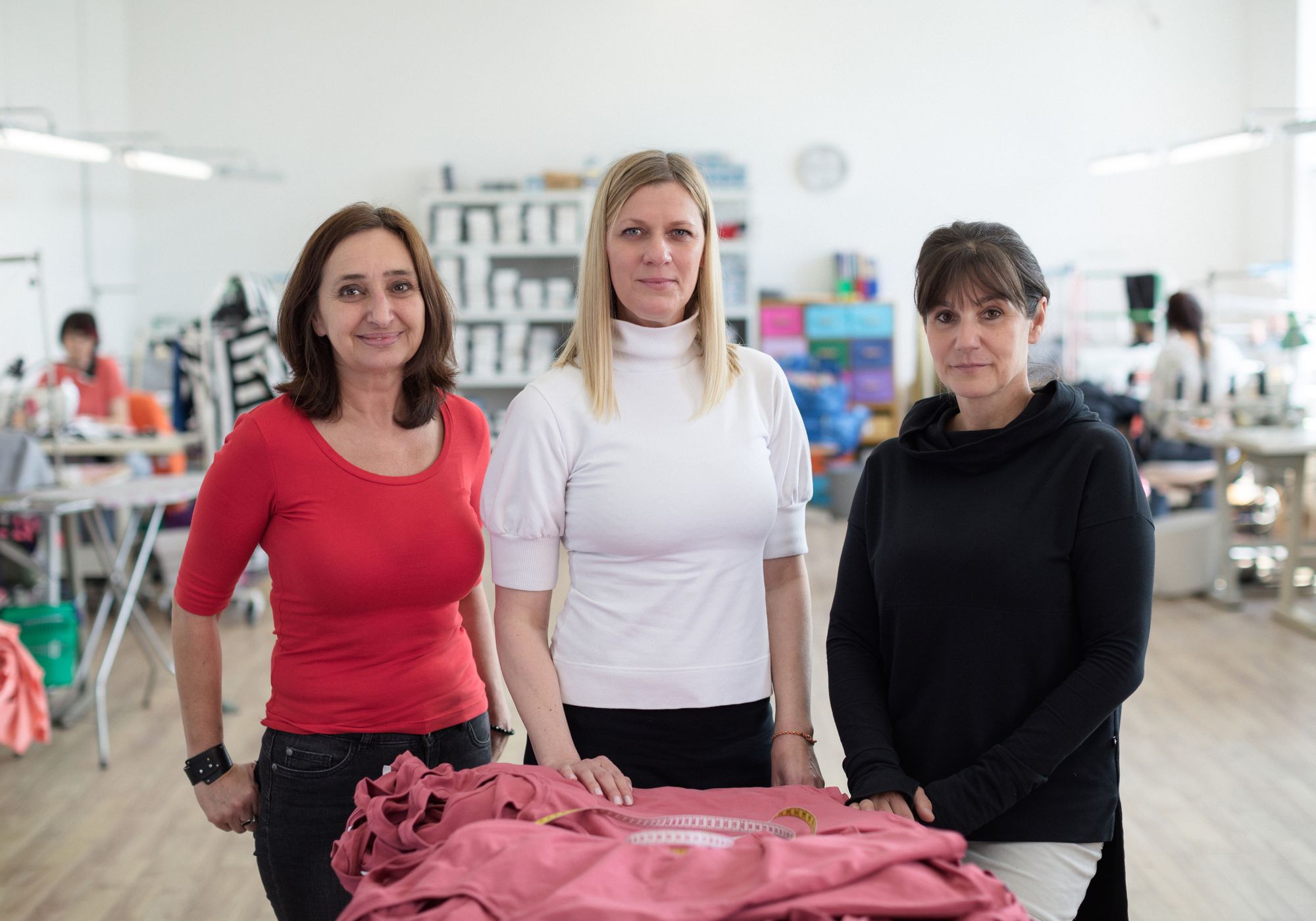
Photos: Balázs Mohai
NON+ | Web | Facebook | Instagram
In our monthly series, we explore where, how and among what circumstances design products are born. There are cases when a designer creates their object themselves, but many times it takes the joint work of the designer and several manufacturers and subcontractors to provide customers with a flawless item. In each episode, we choose a designer from different fields of design and visit the workshops where the actual work takes place.
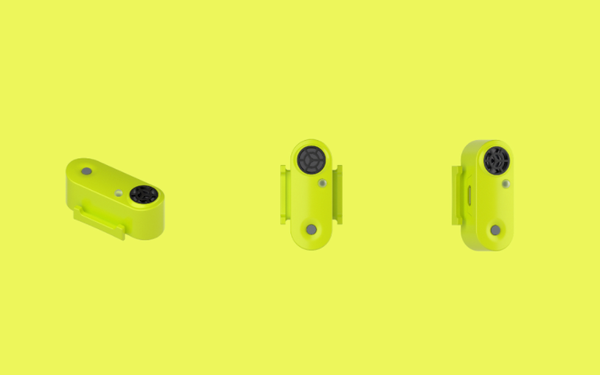
Eco-friendly tick repellent designed in Hungary wins award | A’ Design Award
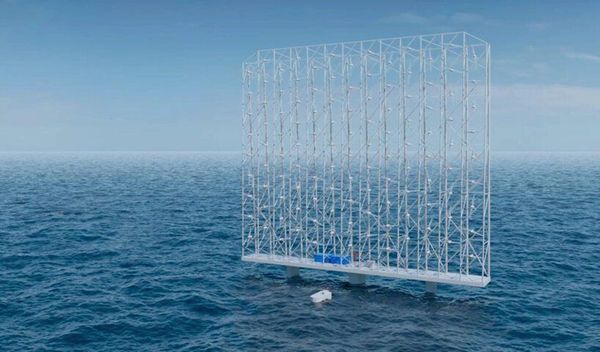
Norwegian company to harvest energy with new floating wind solution
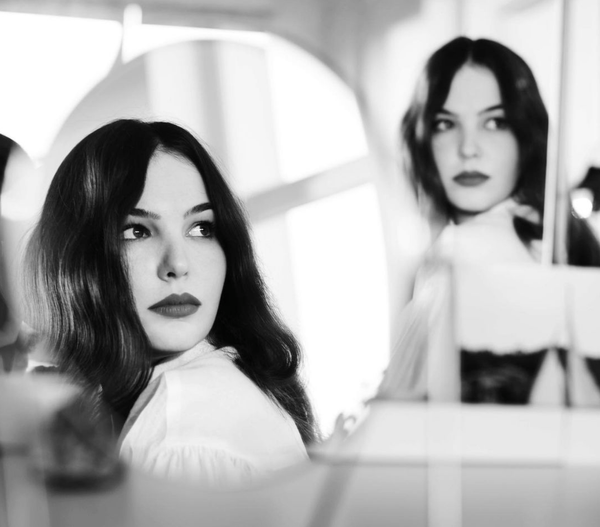