A new chapter opens in the life of the Moholy-Nagy University of Art and Design’s vehicle design program. On the 1st of July, the university’s new automotive design studio, the Mobility Design Lab, will be inaugurated. We talked to András Húnfalvi and Dániel Ruppert, leaders of the program, about the move, and the important moments and experiences in the old studio, as well as about the education within MOME and the future of automotive design. Here’s the first part of our interview with them.
András Húnfalvi and Dániel Ruppert graduated from MOME in 2012 as vehicle designers, and both participated in the joint program between MOME and Mercedes during their university studies. Today, they have their own practices (András Húnfalvi—Flying Objects, Dániel Ruppert—Ustory Branding) and, in addition to their own studio, they co-lead MOME’s automotive design program, carrying on the legacy established 20 years ago by Professor Stefan Lengyel and Professor József Scherer.
Can you tell us about the circumstances of the move: why it became necessary, how it happened and what the overall needs are for this specialization or this type of education?
A. H.: Recently, vehicle design education has undergone a fundamental transformation, especially in the last few years with the pandemic. Even before that, it was already noticeable that there is less relevance for the kind of workshop modeling that was very dominant before, and at the same time, digital technologies have become increasingly important. This is something we are witnessing across the industry and education needs to follow suit. At the same time, we are also seeing that 1:4 scale models are now practically only being produced in universities. At Mercedes, they no longer make models of cars of this size at all during development. In fact, they don’t make any models until the point where they have a few final versions to choose from. These designs are then made—in the same way as the 1:4 models, by the way—in clay, foiled, in 1:4 scale, or presented in the same size using digital technologies, in a projected version that can be viewed with VR glasses.
D. R.: Before the pandemic, typically every two or three weeks, German colleagues would come to do consultations: they would get on a plane, travel here, and be here all day. With the pandemic, it has become a practice to consult online on a weekly or bi-weekly basis, on Zoom or Teams, which is much more efficient. This has introduced a new method of collaboration, making the work much more effective. That’s why these digital technologies like VR are becoming more prominent because they can be shared even remotely.
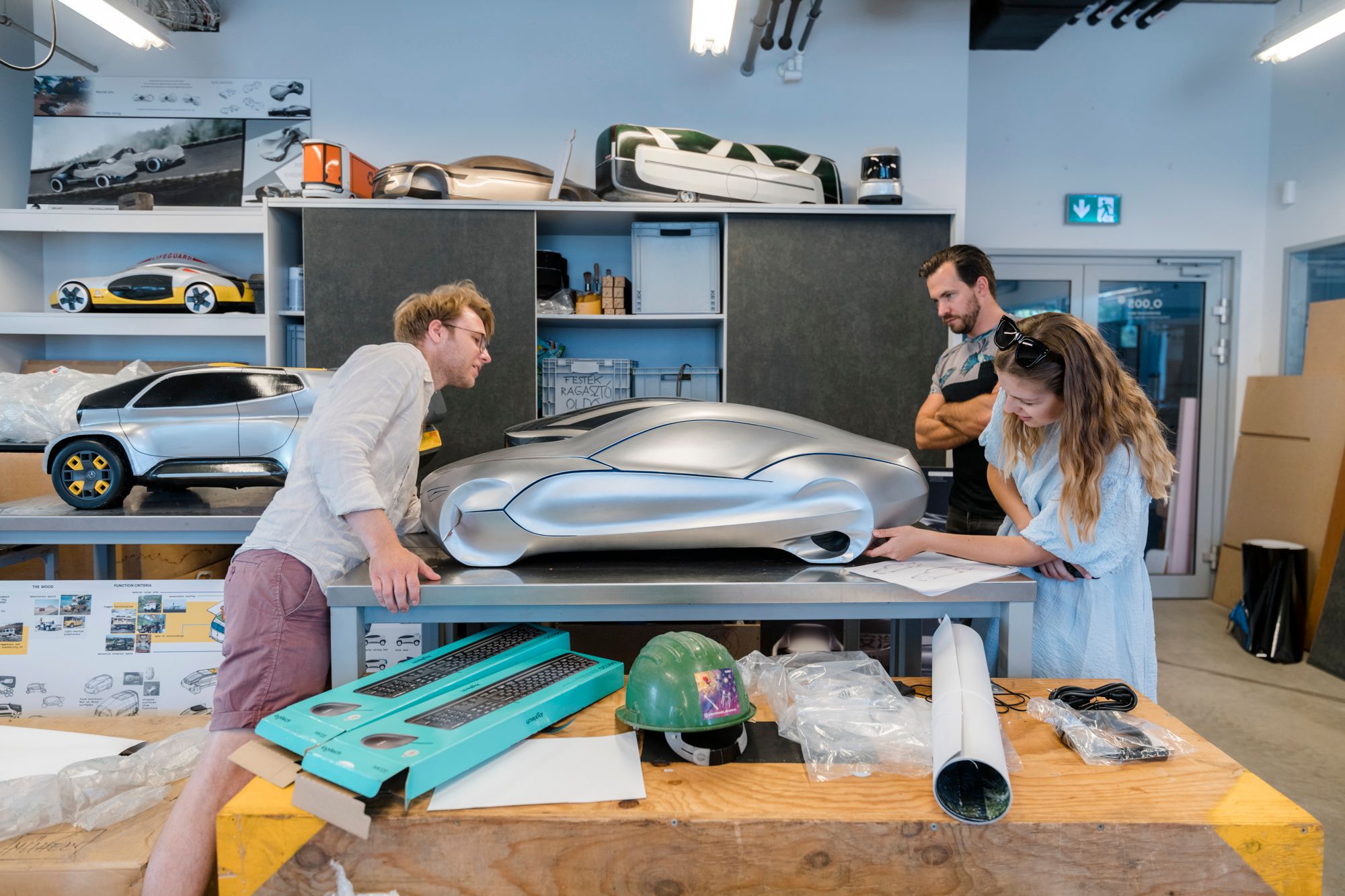
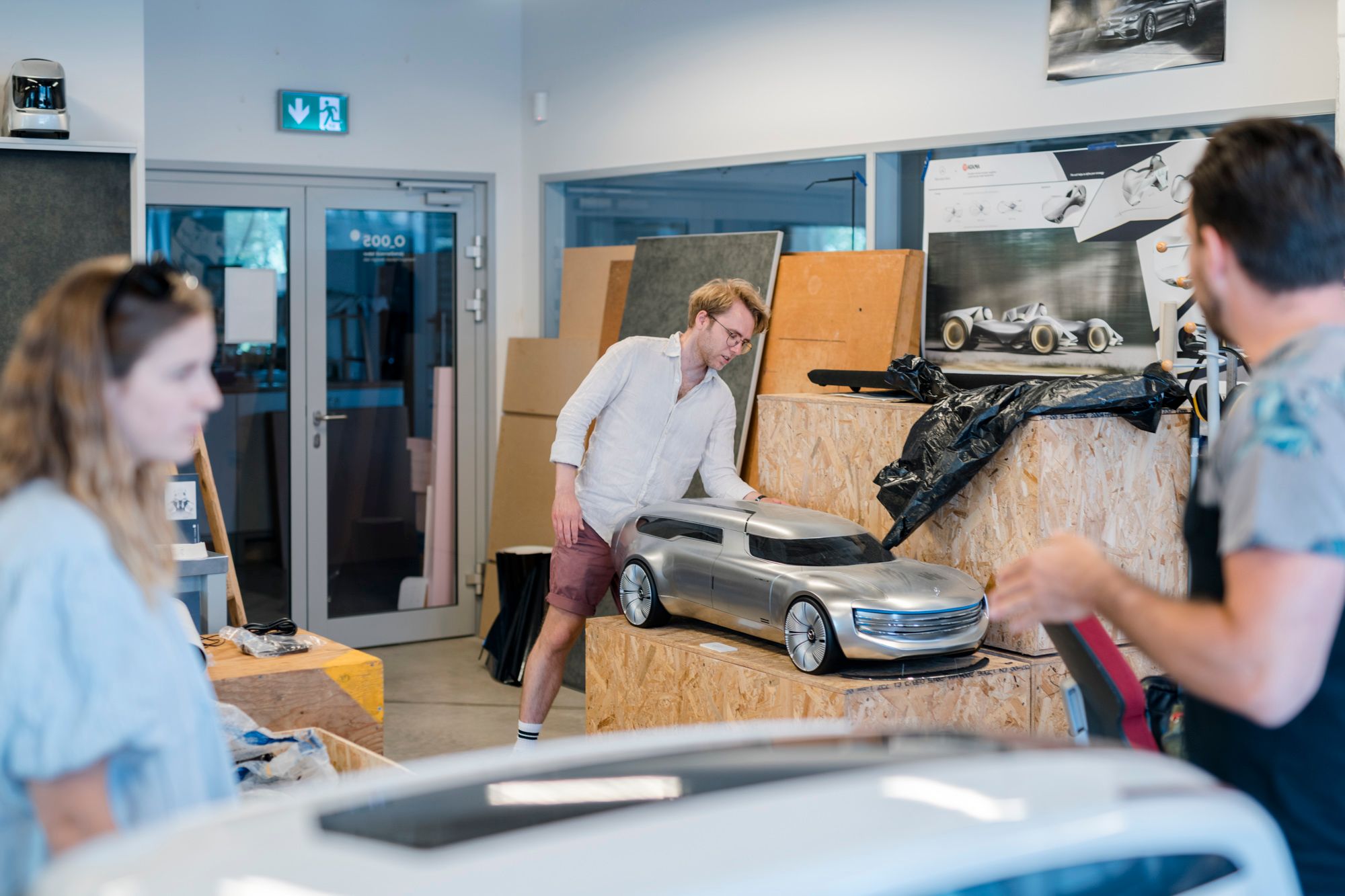
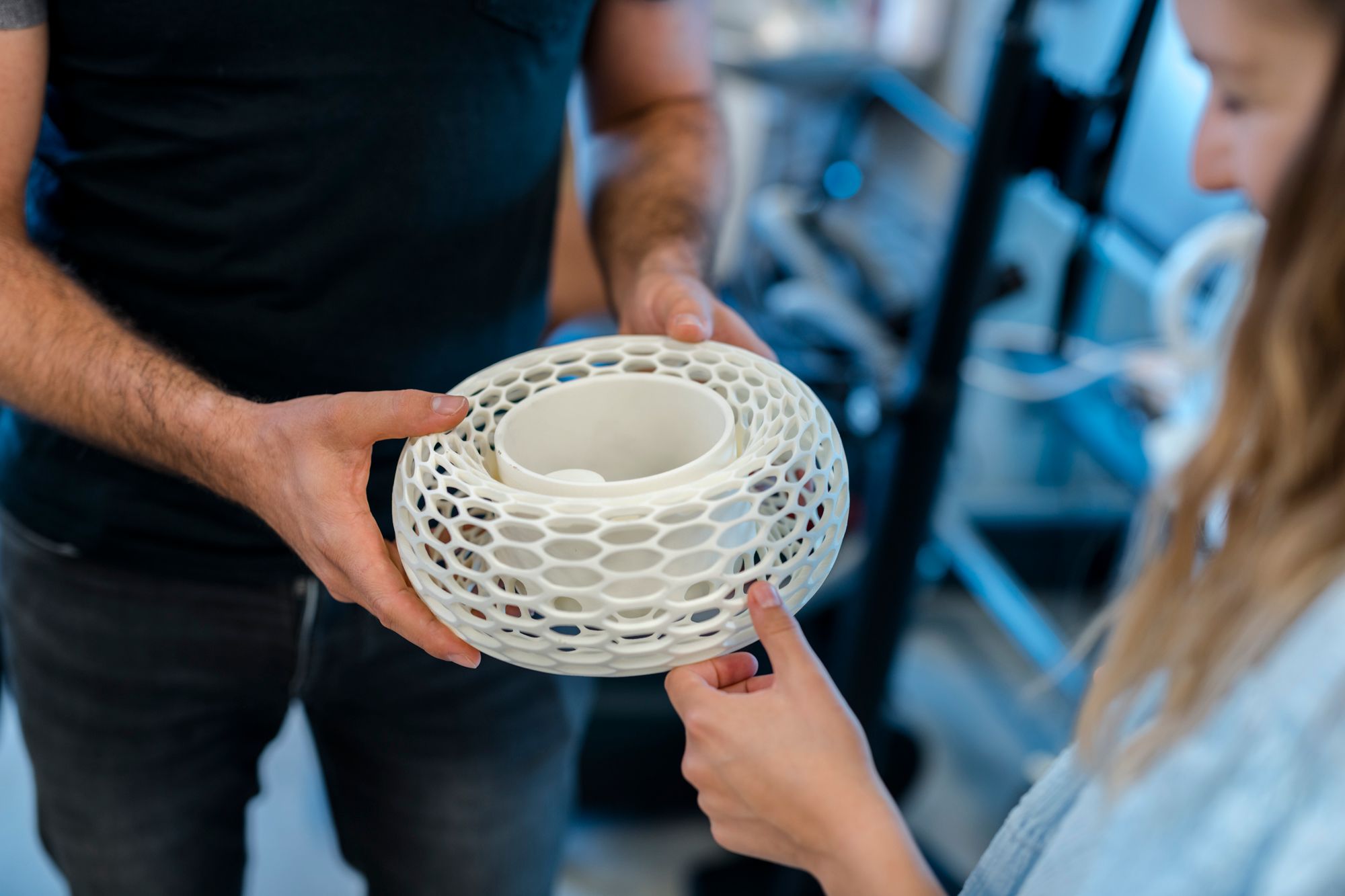
A. H.: Of course, modeling is not going away, because it is an important skill, but it is no longer something that is happening every semester or every year. Also, it’s much more efficient to design and work in a studio-like space with good computers where students can render animations and where you have digital screens and drawing boards.
D. R.: I guess you could say that with the new studio we want to widen the scope for community space and working together. In the new workshop at the lower level of the MOME Base building, we can provide space for this, more space to do collaborations.
What will be different about the new Mobility Design Lab and how much of a milestone is the move for the university?
D. R.: It will be two and a half times the size of the old lab and all the innovative technologies will be provided: VR, rendering machines, animation rendering, 3D printer, large projector, TV, etc. Everything that will help us to model and present quickly and efficiently.
A. H.: It will definitely be a big step forward, and the most important thing is that each of the automotive students will have a space, a little corner of their own where they can put their drawings, their sketches, their posters on the wall; a space that functions a bit like an office.
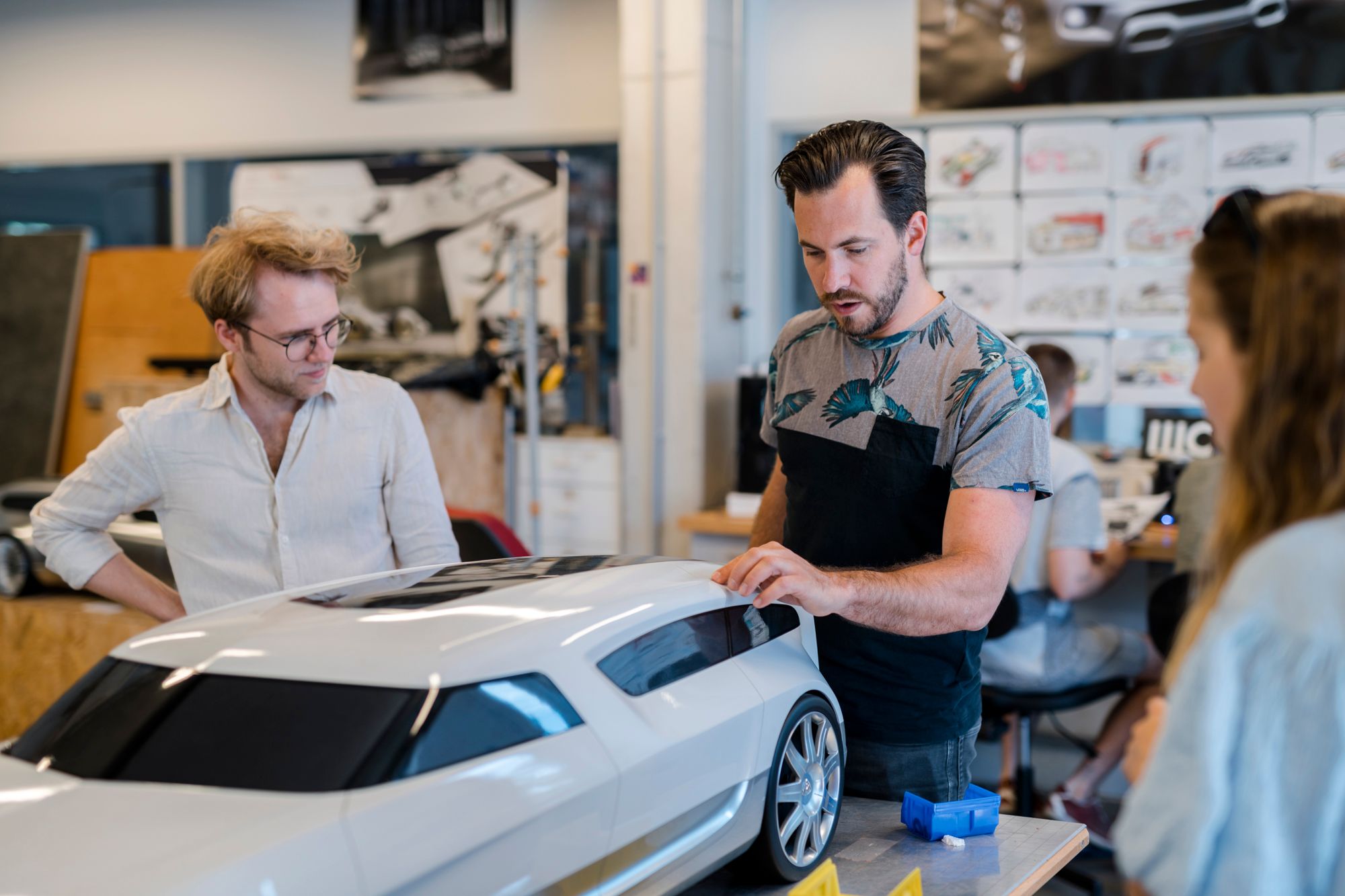
D. R.: Also, students learn most effectively and quickly when they learn from each other in a shared space. If everyone goes home, there is no interaction. It is this intimate teamwork and team spirit that best helps students learn new skills.
A. H.: This also has a great tradition because the automotive team has always been a close-knit crew. It worked very well back then because Mr. József Sherer and the faculty organized it terribly well simply by creating the right framework. They didn’t push us in that direction, there was just a kind of an atmosphere that we were a team here, helping each other. The fact that a second-year undergraduate automotive student and a master’s student who is about to graduate can easily work in the same program is very important in itself, and they can learn a lot from each other. And the outgoing generation actually pulls the new generation forward.
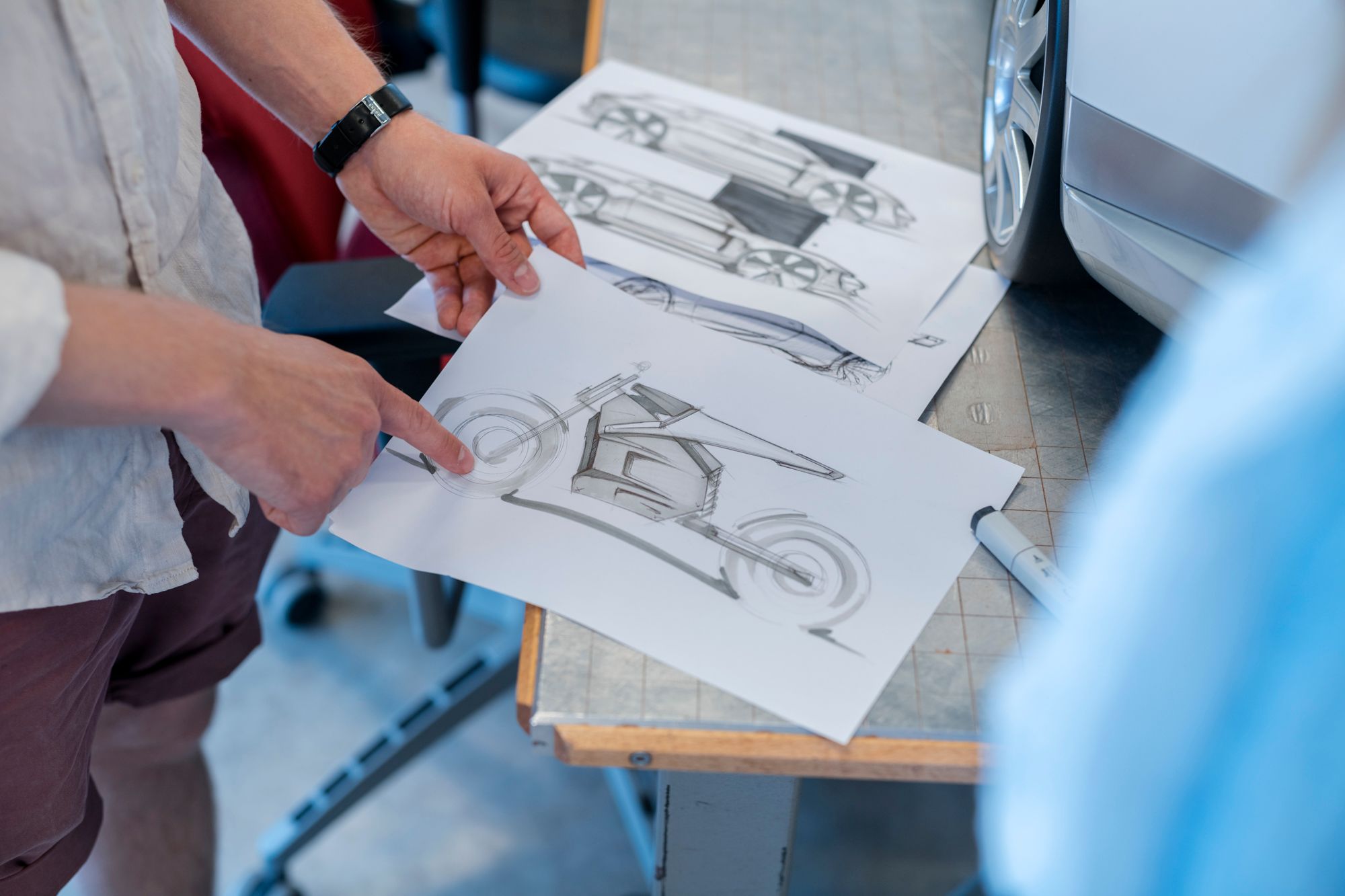
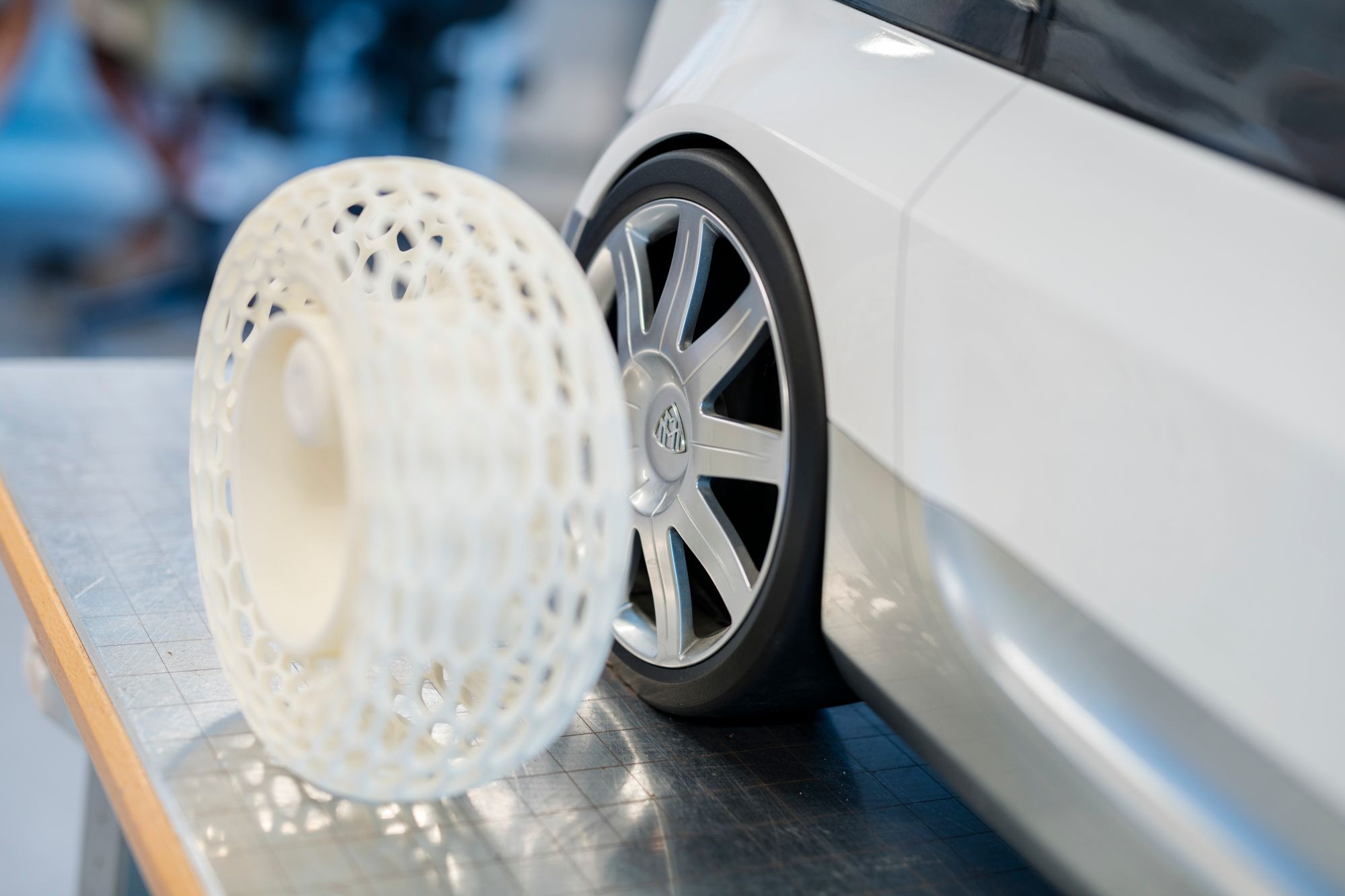
D. R.: It is also very important to mention that students have to regularly give presentations in English. We have German colleagues, so it would be obvious to speak German, but as this is an international company, the standard is to communicate with them in English. The other important thing about the new workshop, apart from the technical stuff, is that we want to expand vehicle design, which in the past was more focused on cars. We want to open this up to a broader spectrum, specifically to the micro-mobility areas, to transport systems.
You have already told us that the old workshop was mainly a place for modeling. What else has happened there over the years?
A. H.: Then we’ll start from even earlier. Originally, the automotive team had a workshop on the old campus, in building C. Actually, it was a modeling-sculpting studio where we too used to make our models back in the day. It was a very run-down little thing, a little space, kind of a passageway, but everybody felt great there because it was our space.
Then when the campus development happened—or actually in the meantime because the workshop building had been completed earlier—a space was created there that was specifically for car modeling, but it wasn’t really suitable for studio work either. We were able to use it relatively well for modeling because the work of four or five students, these 1:4 models could fit in the space, but we didn’t really make use of it. For the kind of modeling that we do, if you have a flexible space like that, you can rearrange it perfectly and for that time you have the tables and the models and everything else there that you need. Then when you’re done, you clean it up and it can be a VR space or a studio again. The old studio wasn’t really suited for that, and we would have needed a little room next to it, where we could have had the computers.
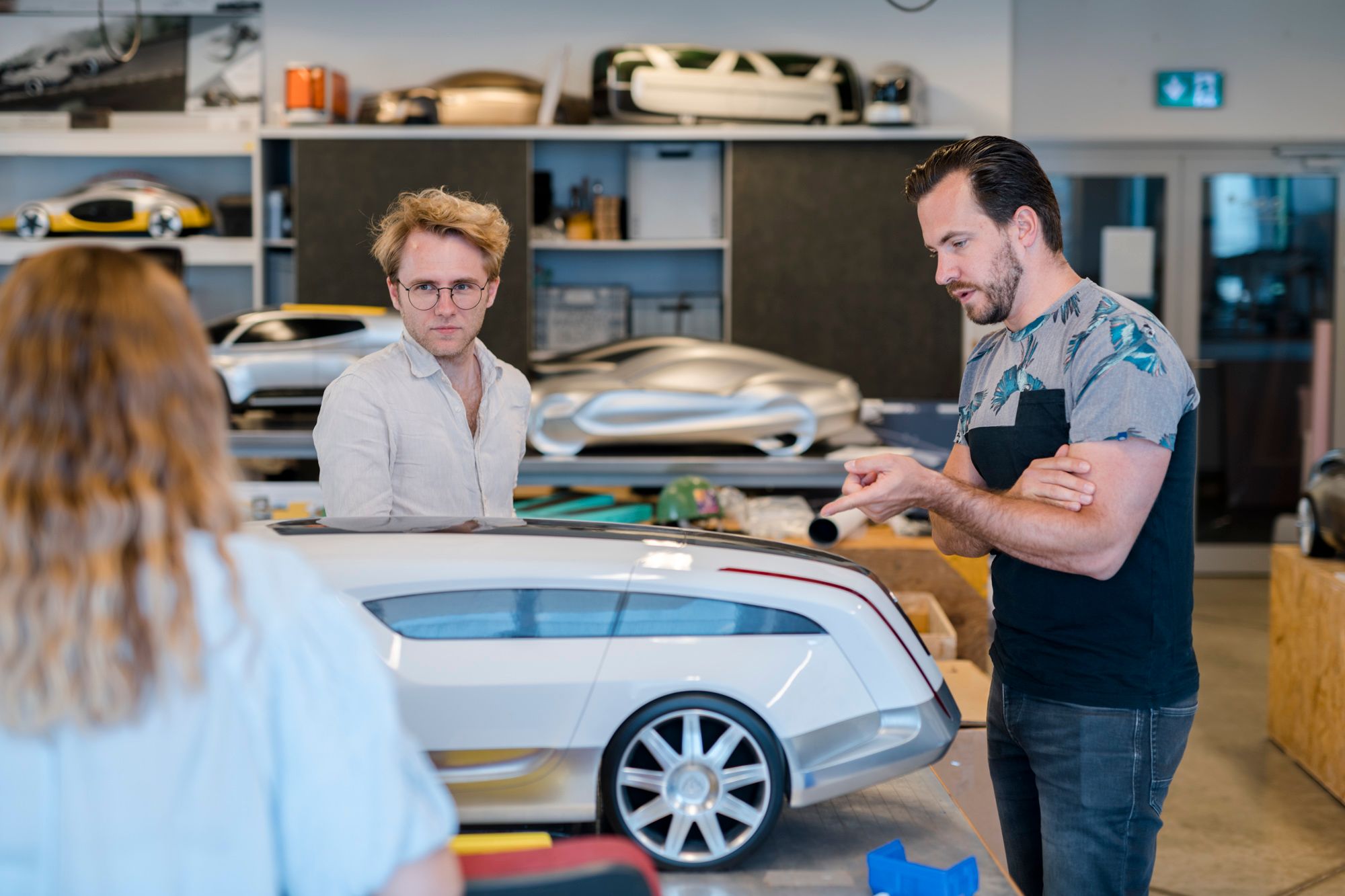
D. R.: Another great memory is how the modelers used to come to visit us regularly. Every spring a team of modelers from Mercedes would come and spend three or four days here with the students, while they were finishing the models they had started. The way to think of it is that the modeling profession is a little bit like sculpture, a separate, specific profession that you study for four or five years. These models are made from a specific industrial clay that you have to learn to work with.
If you’re a car designer, you’re going to dabble in that, but modeling is practically its own trade. It was always a great experience when we did a workshop with our German colleagues at the beginning of the summer. In contrast to the small1:4 models that were made here in the old workshop, the layout of the new space was designed to allow for a walk around a car in VR.
Photos: Máté Lakos
MOME Car Design | Instagram
MOME—Moholy-Nagy University of Art and Design | Web | Facebook | Instagram
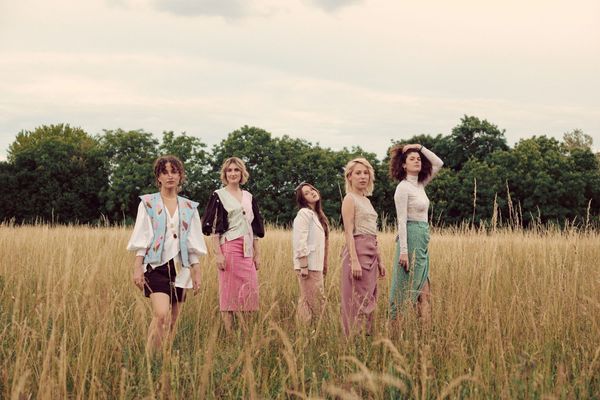
Margaret Island returns to Budapest Park with a mini-festival
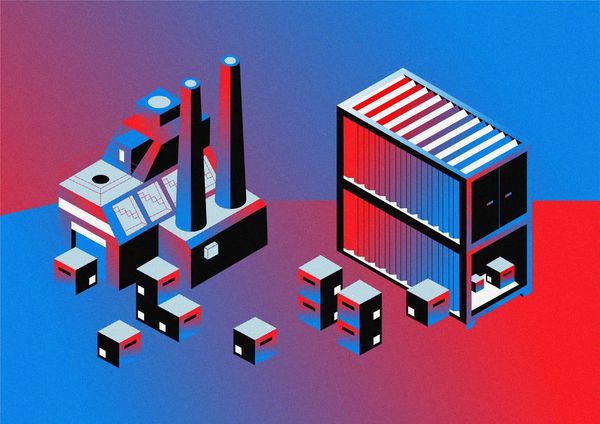
A giant automated e-commerce logistics center will open in Hungary soon
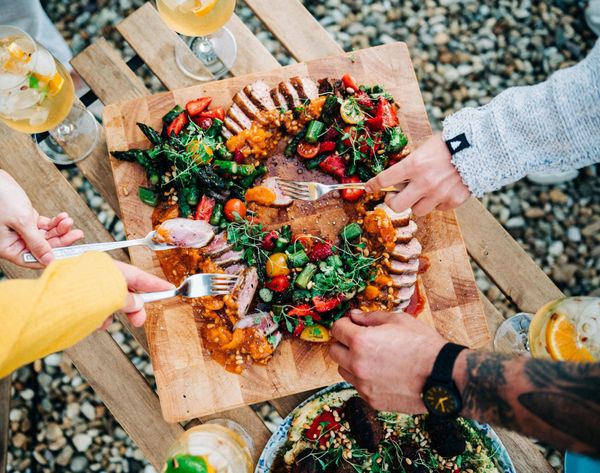