The professional approach of ceramic designer Anita Monori is characterized by focusing on the task on hand: first, she brings up a problem, and then seeks a solution to it from her own perspective. Her main motivation and source of inspiration is being able to create something that people love. She makes her porcelain objects in high quality and with careful precision, therefore, in addition to traditional methods, she also experiments with innovative technological solutions. She first encountered the FabLab Budapest workshop eight years ago and has remained a member of its creative community ever since.
The FabLab Budapest open innovation workshop celebrates the tenth anniversary of its foundation this year. In our new mini-series, we ask the users of the workshop about five topics. This time, we talked with Anita Monori.

Anita founded her own brand called Design by Monori in 2012, which consists of her small-series self-designed and -manufactured porcelain items. She likes minimalistic, clean design, which she sometimes complements with playful graphic elements and other adornments. As part of her scholarship project for the Hungarian Academy of Arts, she is currently exploring the possibilities of combining digital tools with traditional objects: she is working on three new, functional porcelain object collections involving four different types of digital technology. The different technical possibilities of each object serve as a source of inspiration, leaving a mark on their surface.
OBJECT
The first objects I made here were my porcelain pálinka set, parts of which were later used as extra collections and souvenirs for FabLab. To achieve a more precise design, the plaster core was based on a 3D model and made with CNC milling out of plaster sheets cast to the appropriate size. The milled plaster elements had precisely placed grooves on the side and the front, into which I glued laser-engraved rubber elements with small patterns, obtaining the core shape of the embossed objects this way.
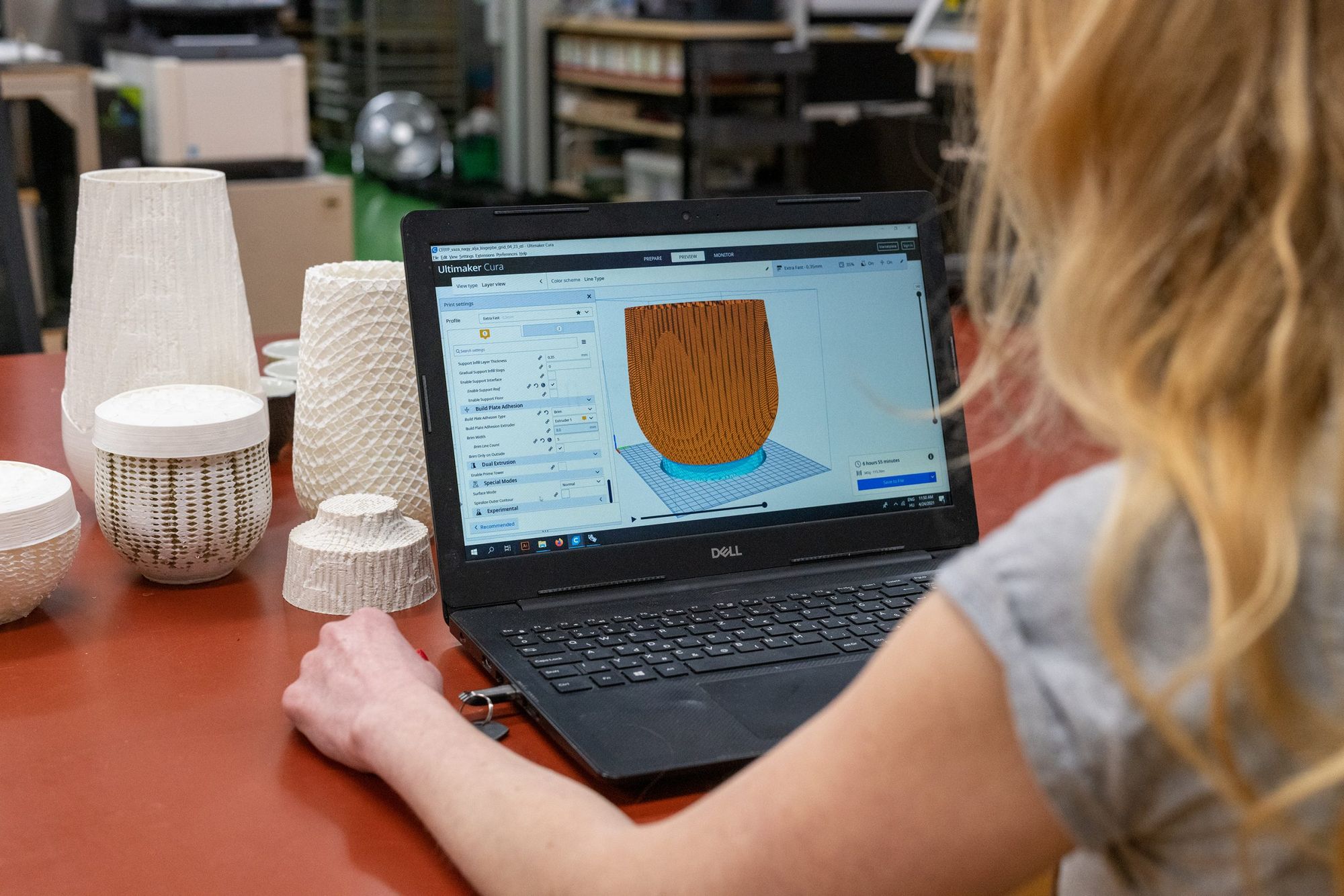
FAVORITE TOOL
Last year—in the first year of my scholarship—I learned how to use the CNC machines in the workshop and, after a lot of experimentation, I created my collection called Hidden Lines. It was important for me to depict the marks of the technological tool on the objects themselves, so I decided to create smooth surfaces based on a given pattern, and combine it with parts where I show the marks of the CNC machine, keeping the rough-out steps and creating a pattern on the objects with this method.
During this experimental period, I also had the opportunity to get familiar with three types of CNC machines. Out of the machines, I liked the Isel GFM 4433 the most, perhaps because this was the machine—and technology— that seemed the most complex to me. I was very afraid of it, because this is considered a piece of industrial equipment, which seemed scary at first. After learning how to handle it, however, I grew to love the machine and the technology itself a lot. It’s a three-axis milling machine with a working area of 330 x 430 millimeters and, importantly for me, it can be equipped with a suction apparatus, which is very useful when milling plaster. I call this machine Izelke, and I think that the founder of FabLab, Dávid simply calls it “Izel” or “Little Izel”.
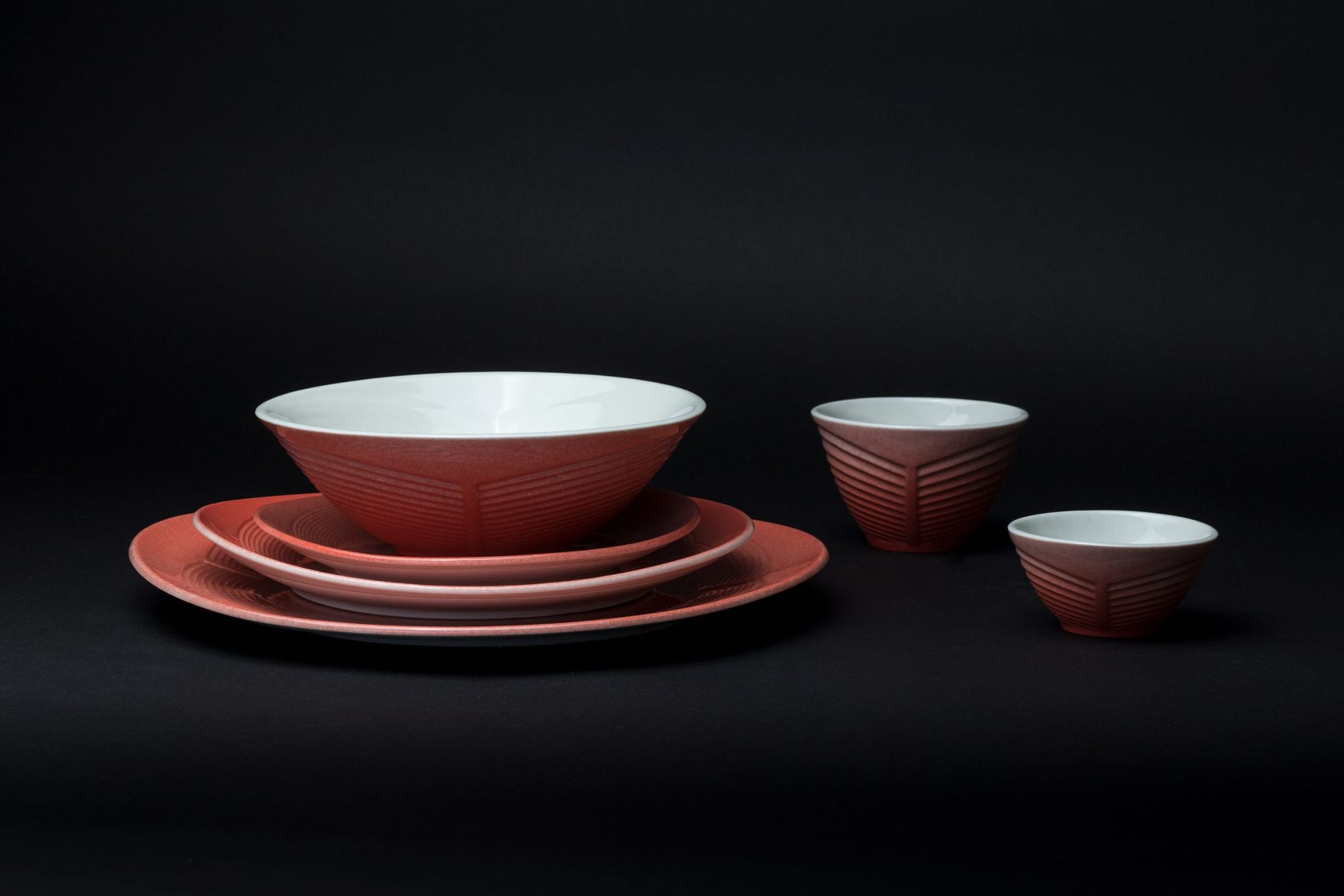
ENCOUNTER IN THE WORKSHOP
I wouldn’t be able to narrow this down to a single person, because I was lucky enough to meet several inspiring people at FabLab, both employees and workshop users. What is very inspiring to me, however, is the diversity of people who come here: people from very different professions can meet here and chat casually about an object, shape or technology. These conversations are always very interesting and result in new insights since we approach the same thing from completely different perspectives.
INSPIRATION
In my opinion, learning about and using digital technologies can make the process of object creation much easier, as machine production is often more precise and accurate than manual work. Any new technology can lead to further implementation solutions: nevertheless, I don’t think we should use them in every case, but it is definitely worth learning about them, exploring new possibilities, rethinking the benefits they provide and incorporating these into the process of object creation.

EXPERIMENTATION
I am currently working with FDM-type 3D printing to experiment with surfaces and shapes—I want to print larger shapes with this method in the near future. I will use parts of these and the surfaces of the 3D-printed filling structures to create my new collection. One of the important directions of my scholarship project is how the surfaces created during machine shaping with all their possible defects affect the shape, surface and details of the finished object. Next year, I’d also like to work with resin-based SLA printing, and the possibilities of 3D scanning and laser cutting are also interesting to me.
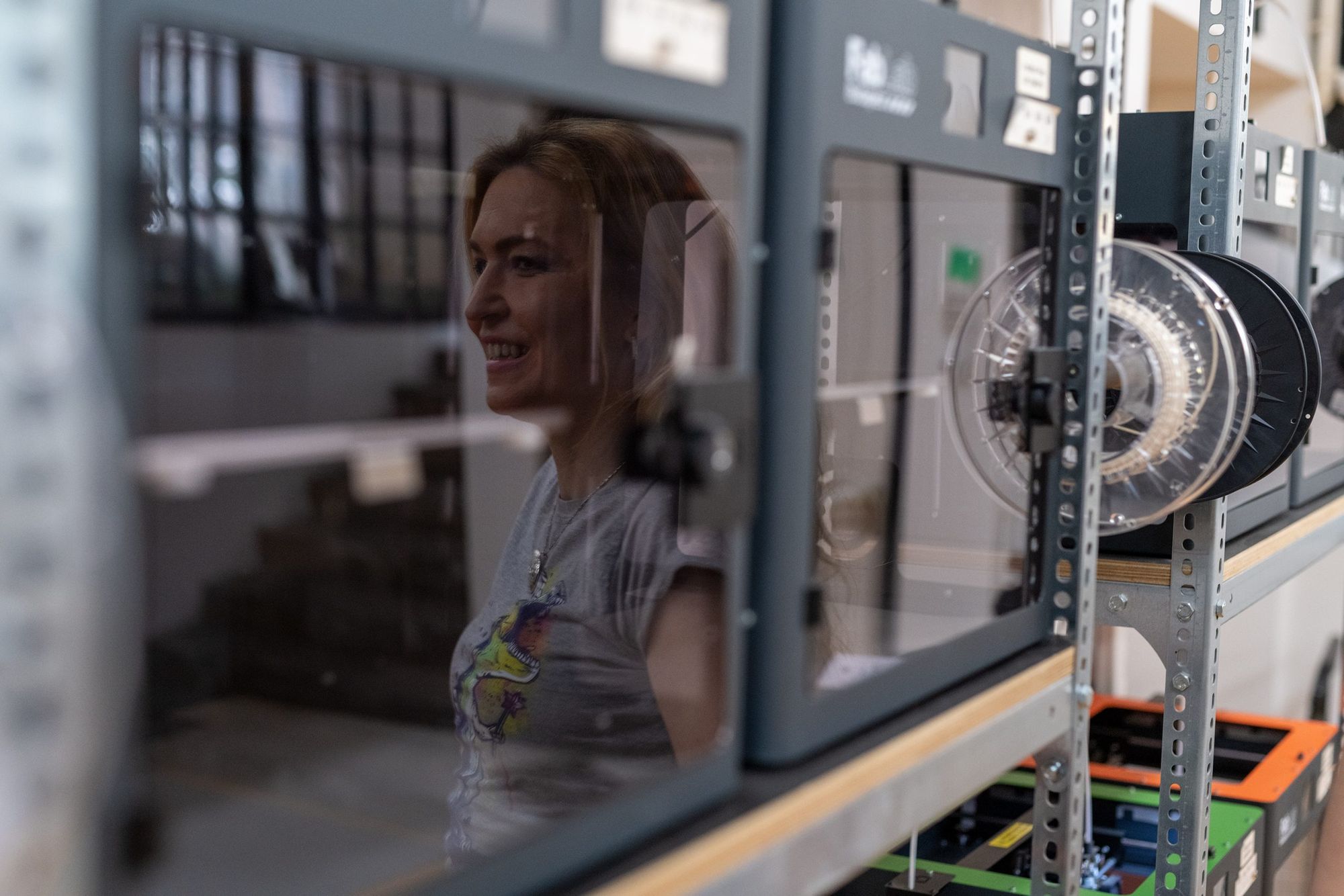
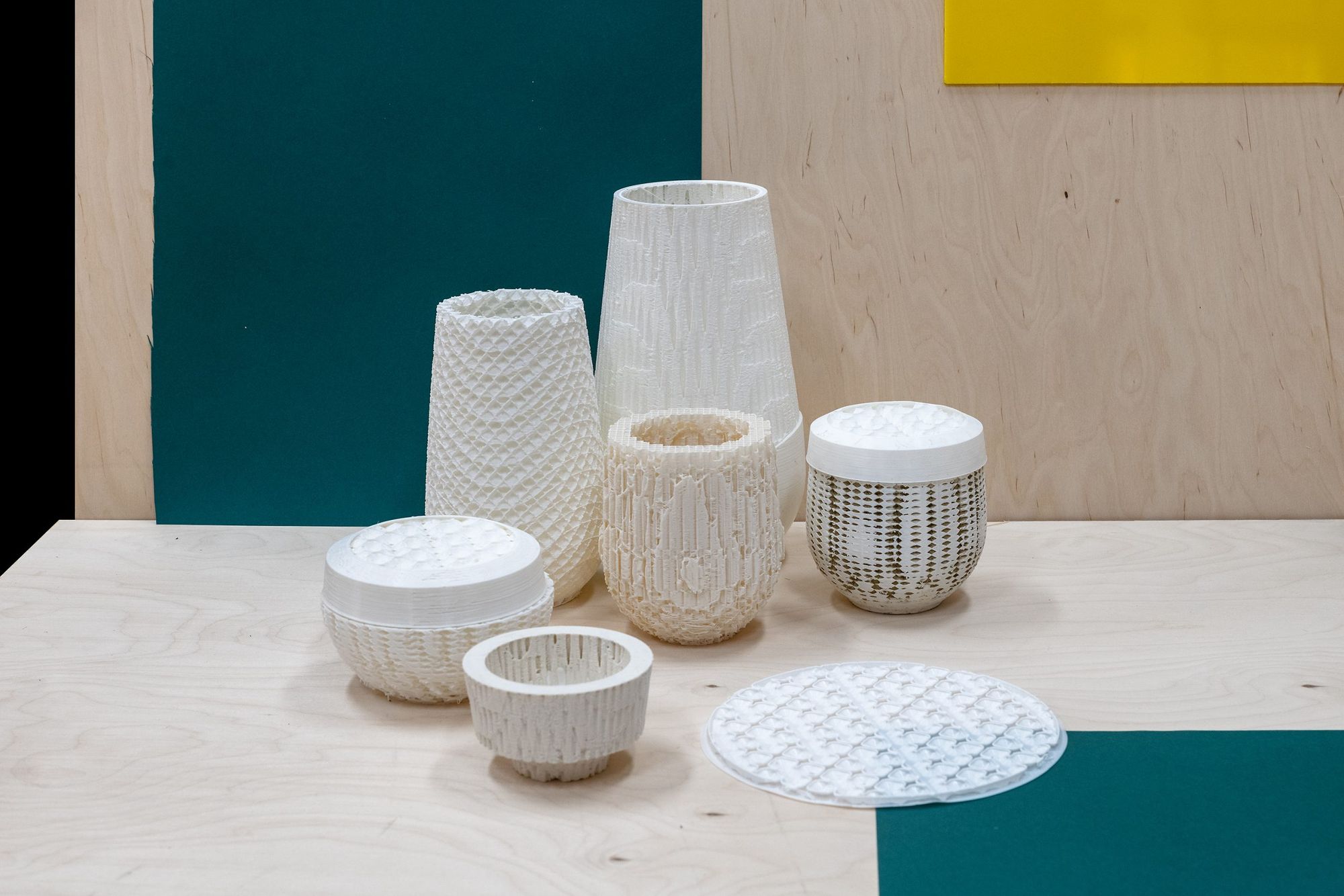
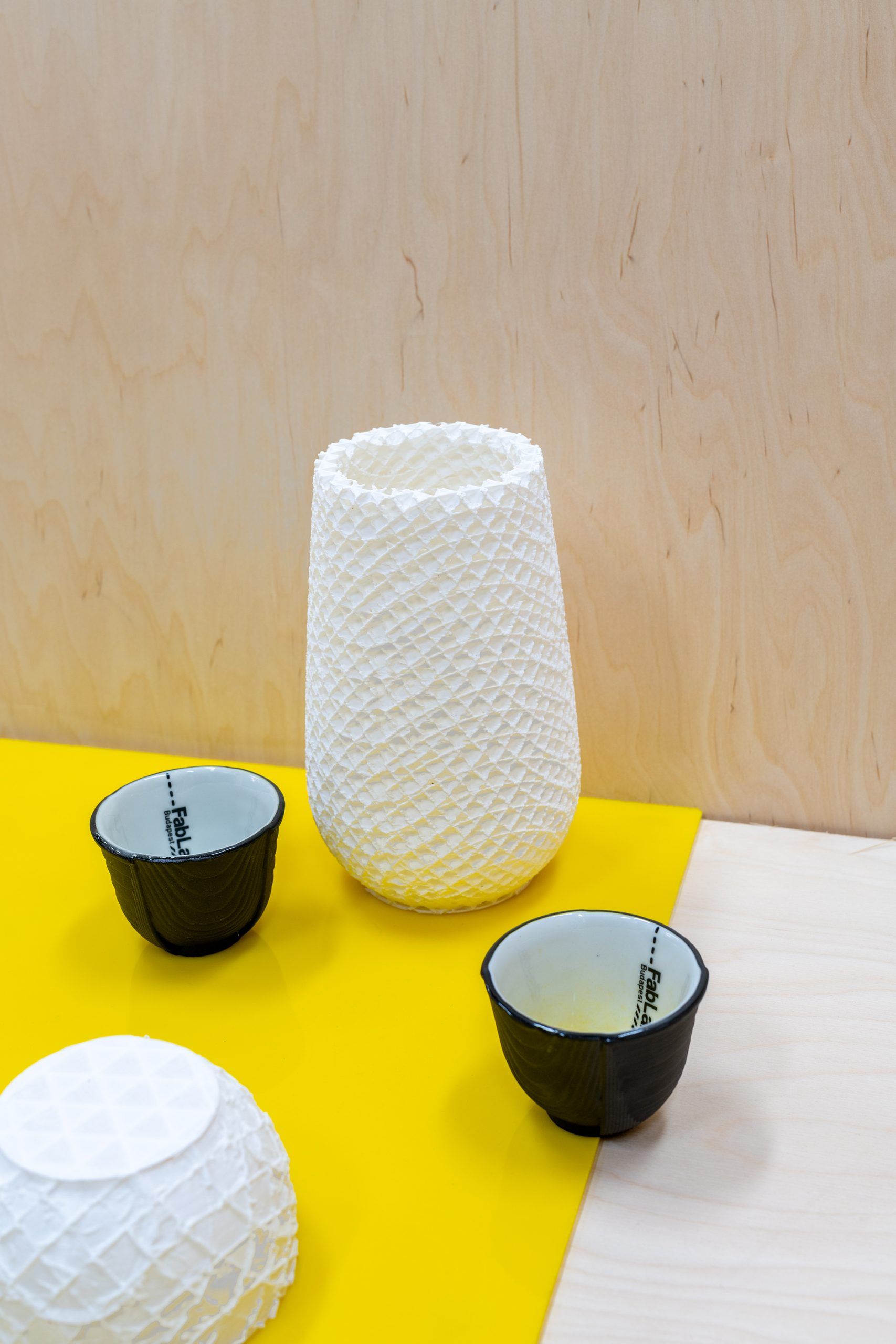
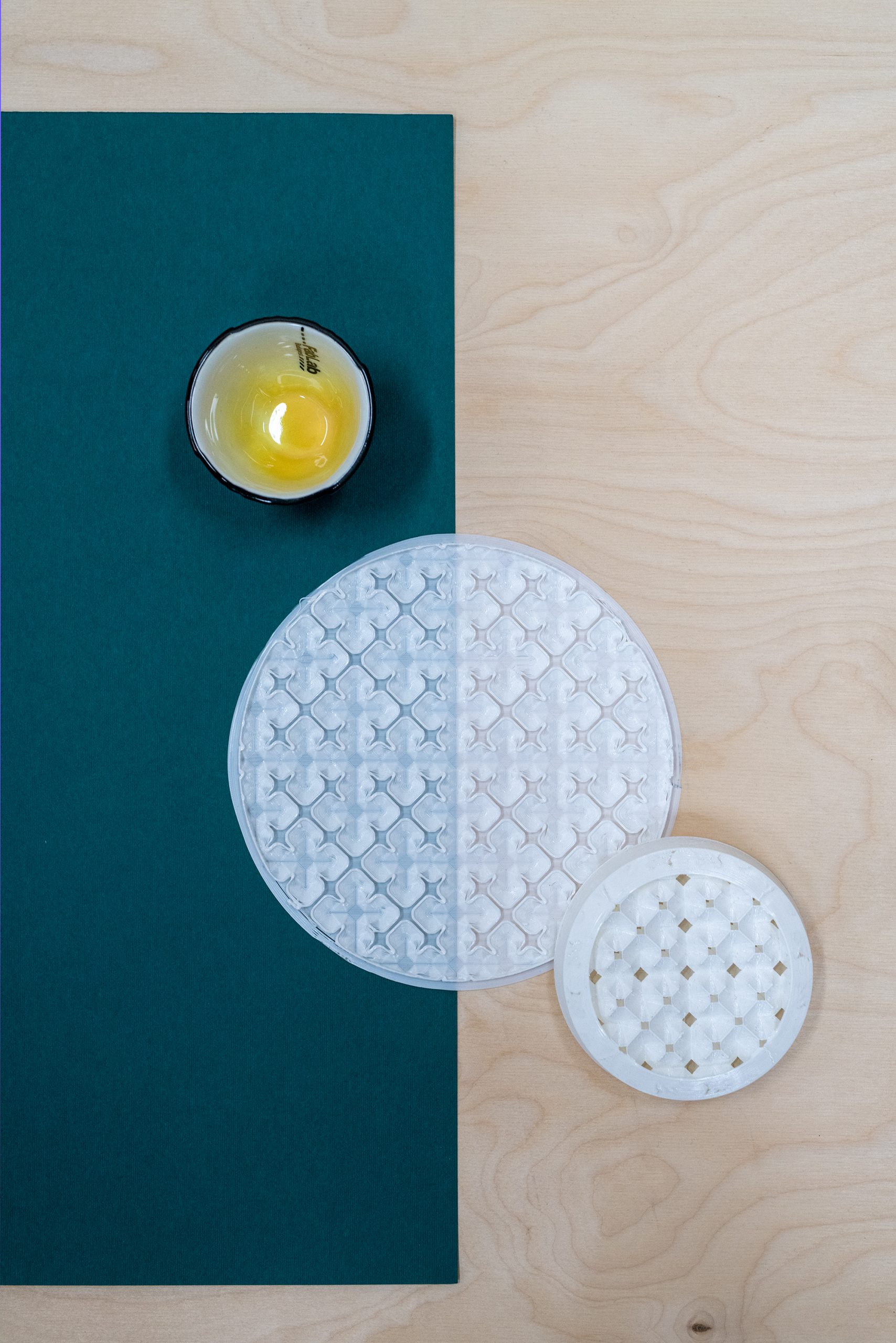
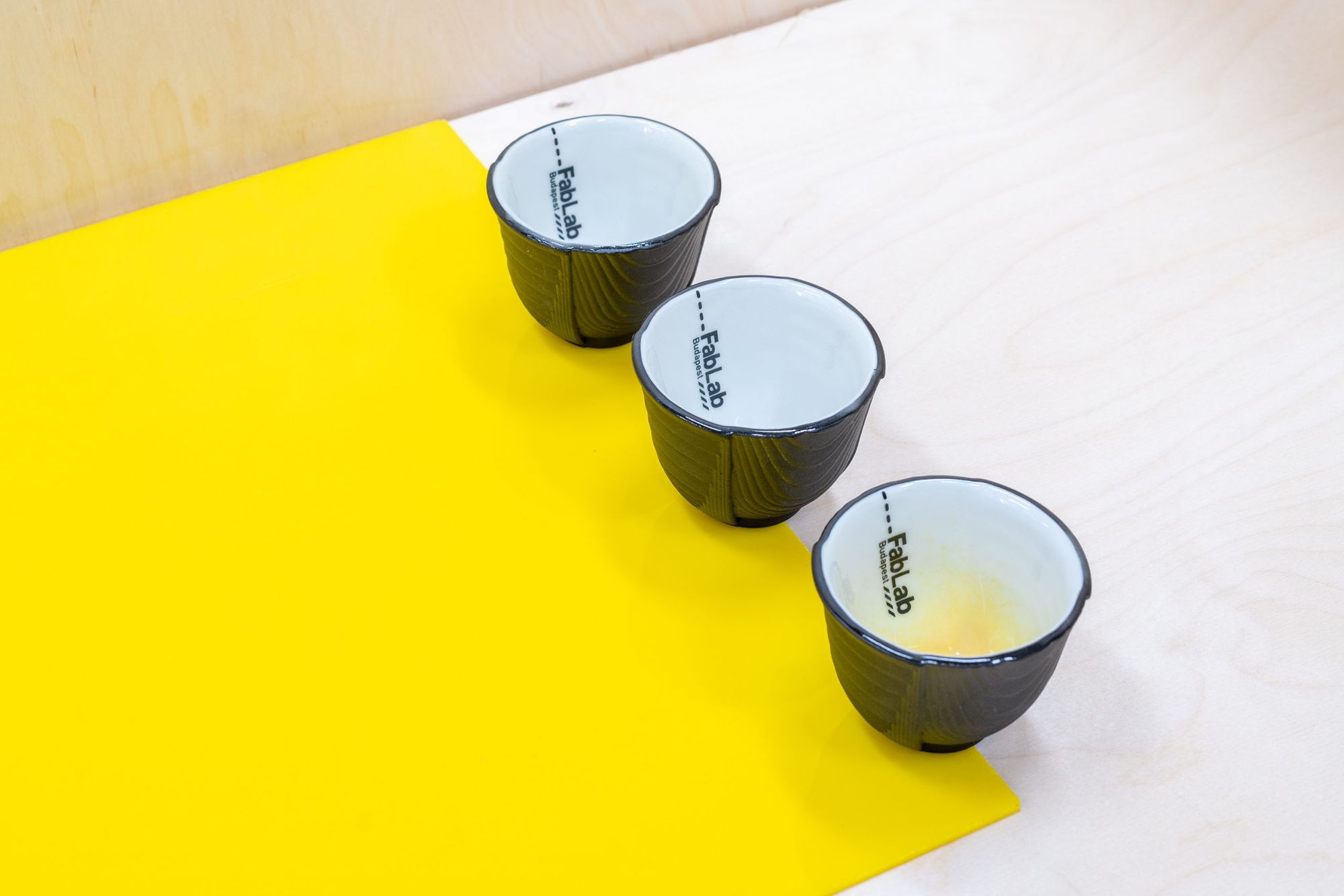
Photos: Balázs Csizik
Anita Monori | Web | Facebook
FabLab Budapest | Web | Facebook | Instagram
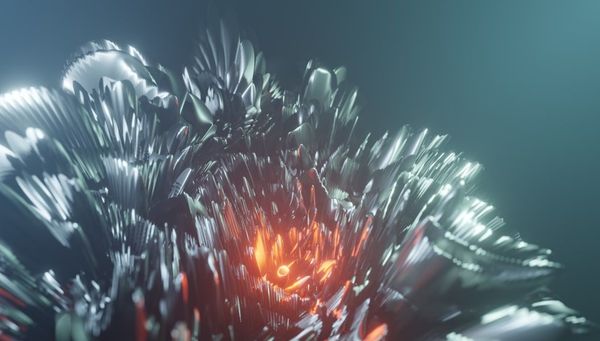
New EP with utopistic sound and visuals | ONAKOM
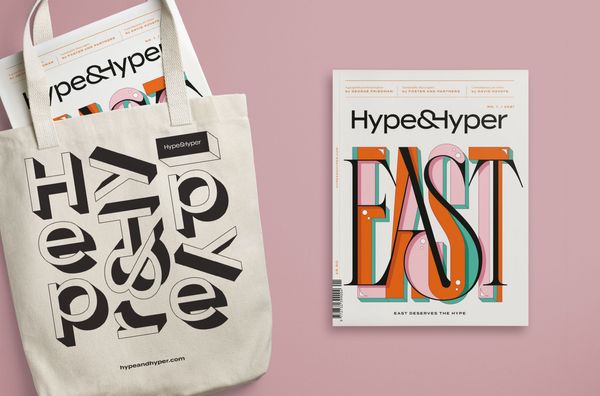
The first printed issue of Hype&Hyper is now available for pre-order!
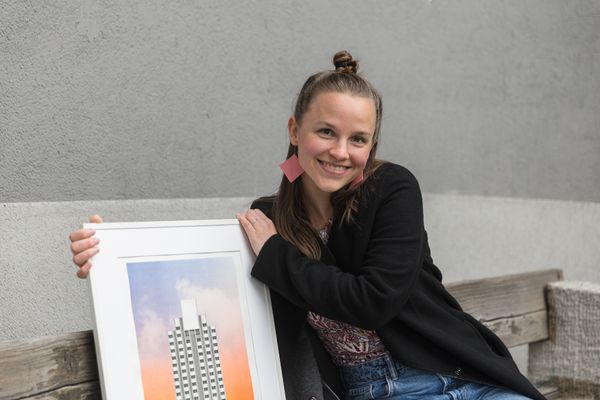